Venus Aerospace’s Detonation Rocket Engine Advances Hypersonic Propulsion
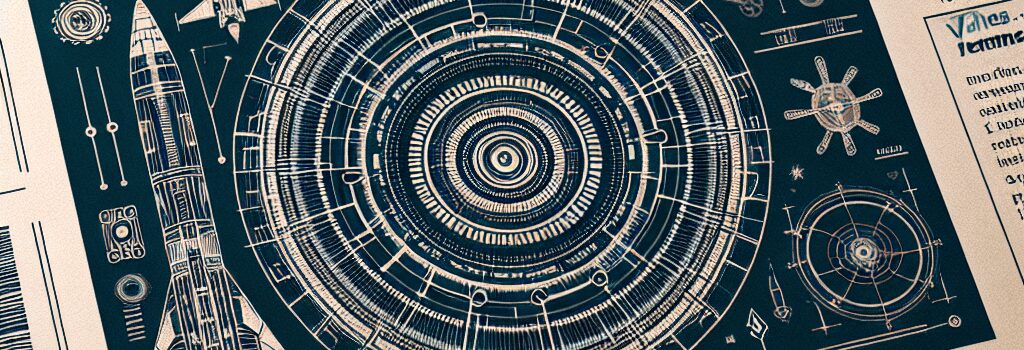
An American First in Advanced Propulsion Testing
On May 14, 2025, Venus Aerospace completed the first U.S. flight test of a rotating detonation rocket engine (RDRE) at Spaceport America in New Mexico. Powered by a 2,000-pound thrust-class demonstrator, the vehicle lifted off from a rail launcher and sustained thrust for roughly 30 seconds. While the subsonic test did not break Mach 1, engineers gathered critical performance data confirming stable detonation waves in an operational flight environment.
Technical Deep Dive: The Mechanics of Rotating Detonation
- Detonation Wave Propagation â~ In a conventional rocket, propellant mixes under pressure and burns subsonically. In contrast, an RDRE sustains continuous detonation waves traveling around an annular combustion chamber at roughly 2,000 m/s, producing a series of supersonic shock fronts that enhance thermal efficiency.
- Injector and Chamber Design â~ Venus Aerospace uses a counterflow swirl injector array feeding liquid methane and liquid oxygen at 8 MPa total inlet pressure. Precise injection timing maintains a stable single-wave detonation mode, avoiding mode-jumps that degrade performance.
- Performance Metrics â~ Ground tests have shown a 10–15% increase in theoretical specific impulse (Isp) over equivalent gas-generator cycle engines. Measured chamber pressures reached 12 MPa, with combustion efficiencies above 98% during steady-state operation.
Comparative Performance Analysis
Rotating detonation engines promise higher thrust-to-weight ratios and improved propellant utilization. A typical gas-generator methane/LOX engine at this scale yields around 330 s Isp, whereas RDREs could target 365–380 s. Reduced turbine power requirements and simpler plumbing also lower system mass by an estimated 15%.
Applications and Partnerships
Venus Aerospace is engaging with U.S. defense agencies, NASA, and several aerospace primes under confidential agreements. Early use cases include hypersonic boost phases for tactical missiles, upper-stage boosters for small satellites, and rapid global logistics platforms. A senior Air Force Research Laboratory (AFRL) official noted that RDRE technology aligns with ongoing DARPA and Operational Fires programs aiming to field Mach 5+ systems within this decade.
Industry Landscape and Global Context
Several international players, including research teams in China, Russia, and Europe, have demonstrated bench-scale RDREs. However, Venus Aerospace’s flight marks the first high-thrust, in-flight validation. Academic groups at University of Central Florida and Technical University of Munich continue investigating multi-wave modes and hydrogen-based variants, highlighting a growing global R&D focus on detonation-based propulsion.
Future Challenges and Development Roadmap
- Thermal Management â~ Detonation-driven heat fluxes exceed those in conventional chambers by up to 40%, demanding advanced regenerative cooling channels and ceramic matrix composites.
- Combustion Stability â~ Scaling from 2,000 to 50,000 pounds of thrust will require multi-wave synchronization and active control systems to prevent destructive pressure oscillations.
- Regulatory and Integration â~ Hypersonic flight raises new certification hurdles for commercial aviation regulators, as well as noise and sonic boom mitigation issues over populated areas.
Outlook: Toward Hypersonic Commercial Travel
While orbital and suborbital market entry is expected within 3–5 years, Venus Aerospace’s long-term vision remains point-to-point hypersonic transport capable of carrying a dozen passengers anywhere on Earth in under two hours. Continued government funding, materials research, and successful scale-up tests will be vital to realize this ambition.