Stellantis Ends Hydrogen Fuel Cell Development
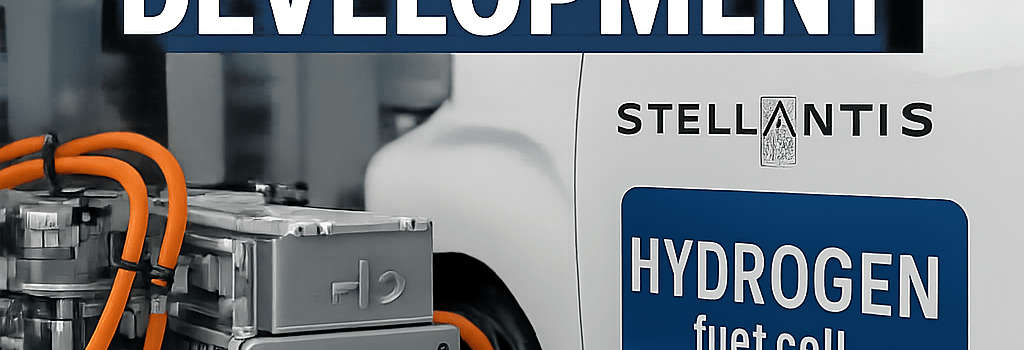
Introduction
In July 2025, Stellantis quietly pulled the plug on its light-, medium- and heavy-duty hydrogen fuel cell electric vehicle (FCEV) program, confirming what many in the industry have long suspected: hydrogen remains an expensive, inefficient and infrastructure-challenged solution for road transport. This decision, affecting planned commercial vans due in Europe later this year, underscores the mounting technical and economic hurdles that FCEVs continue to face, and highlights Stellantis’s renewed focus on battery electric and hybrid powertrains.
Technical Limitations of Hydrogen Fuel Cells
Hydrogen’s appeal hinges on rapid refueling and zero tailpipe emissions, but the reality is far less compelling once you unpack the physics and infrastructure requirements.
- Volumetric Energy Density: At 70 MPa (10,000 psi), compressed hydrogen stores only ~5.6 MJ/L, compared to ~32 MJ/L for diesel or gasoline. Even liquid hydrogen at –253 °C achieves only ~8.5 MJ/L, requiring heavy cryogenic tanks and complex insulation.
- Fuel Cell Stack Cost: Current proton exchange membrane (PEM) stacks cost ~$70–100 per kilowatt, far above the U.S. Department of Energy’s 2025 target of ~$40/kW. Precious metal catalysts (Pt, Ir) still dominate, keeping mass-production costs high.
- Electrolysis Efficiency: Green hydrogen produced via PEM electrolysis achieves 60–70% round-trip efficiency, versus 85–90% for lithium-ion battery charging. Combined with 50–60% fuel cell conversion efficiency, the end-to-wheel efficiency falls below 35%.
- Compression & Cooling Energy: Compressing hydrogen from 1 to 700 bar consumes ~10–15% of its energy content. Liquefaction requires even more, up to 30% of the input energy, while boil-off management adds further losses.
Infrastructure and Market Adoption Challenges
Without a robust refueling network, FCEVs cannot achieve meaningful market penetration. According to the International Energy Agency (IEA), there are fewer than 600 hydrogen stations worldwide, with just 53 active sites in California—a leading market—serving fewer than 15,000 FCEVs.
- Station Installation Costs: A single 700 bar station can cost $2–3 million, driven by high-pressure compressors, storage vessels and safety systems.
- Logistics Complexity: Hydrogen distribution requires specialized cryogenic tankers or on-site electrolyzers, each with CAPEX and OPEX burdens that far exceed those of diesel or electric charging infrastructure.
- Safety & Regulatory Hurdles: Hydrogen’s low ignition energy and wide flammability range (4–75% by volume in air) demand extensive sensor networks, leak detection and flame arrestors—factors that complicate rollout in urban and residential zones.
Comparative Efficiency and Lifecycle Emissions
Even when produced from renewable sources, hydrogen’s carbon footprint can be comparable to or worse than direct electrification. A typical green hydrogen pathway involves:
- Electrolysis powered by wind or solar (60–70% efficiency).
- Compression/liquefaction losses (10–30%).
- Fuel cell conversion (50–60%).
By contrast, grid-charged battery electric vehicles (BEVs) achieve 73–85% efficiency from source to wheels, with rapidly declining lifecycle emissions as the grid decarbonizes.
Expert Opinions and Industry Response
“In a context where the Company is mobilizing to respond to demanding CO₂ regulations in Europe, Stellantis has decided to discontinue its hydrogen fuel cell technology development program,” said Jean-Philippe Imparato, COO for Enlarged Europe. “The hydrogen market remains a niche segment, with no prospects of mid-term economic sustainability.”
Industry analysts at BloombergNEF and the Fraunhofer Institute concur that FCEVs may find a future in heavy-duty trucking or off-grid applications, but that light-duty and commercial vans are better served by battery or plug-in hybrid drivetrains. Toyota and Hyundai continue to invest selectively, but global FCEV sales remain below 30,000 units per year.
Future Outlook and Strategic Shifts
Stellantis plans to redeploy its hydrogen R&D teams to accelerate its STLA Large and STLA Medium BEV platforms, alongside the ongoing roll-out of hybrid systems across its 14 brands. The company’s €30 billion electrification budget through 2025 will prioritize:
- Next-generation 800 V battery architectures for faster charging.
- Solid-state electrolytes to improve cell safety and energy density.
- Advanced power electronics to reduce system weight and cost.
While hydrogen retains potential in niche segments—such as stationary power and maritime transport—its viability in mainstream road vehicles remains in doubt unless dramatic breakthroughs occur in catalyst materials, storage media and distribution networks.
Key Takeaways
- Hydrogen’s low volumetric density and high infrastructure cost limit its competitiveness vs. BEVs.
- Lifecycle efficiency of FCEVs rarely exceeds 35–40%, compared to 75–85% for BEVs.
- Stellantis will shift investments to battery and hybrid platforms, redeploying hydrogen teams internally.