Starship’s Ninth Flight: Successes and Future Upgrades
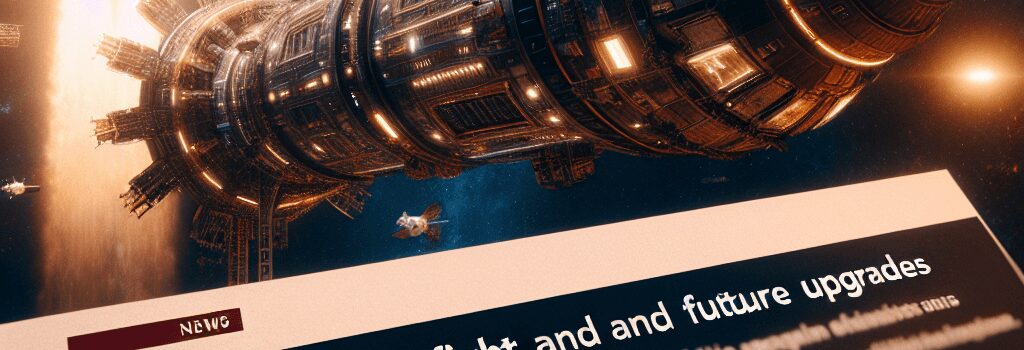
By Stephen Clark – May 28, 2025
Overview
On Tuesday evening, SpaceX launched the ninth test flight of Starship from its South Texas Starbase, marking the first time the Super Heavy booster was reflown. Despite full-duration burns on both stages and nominal ascent, the mission ultimately succumbed to a main tank pressure loss during coast, triggering a tumble and uncontrolled reentry over the Indian Ocean. While the flight avoided earlier propulsion failures, it unveiled fresh technical hurdles in propellant management and thermal protection.
Flight Profile and Key Milestones
- Lift-off: 6:35 pm CDT (23:35 UTC) after a brief hold; 33 sea-level Raptor engines ignited, delivering ~18.6 MN of thrust.
- Stage Separation: Occurred ~150 seconds after launch; Super Heavy returned for a splashdown dunk, while Starship’s upper stage continued to orbit insertion burn.
- Insertion: Nine minutes in, Starship achieved planned T-O**C (tail-off cutoff) but remained sub-orbital by ~200 m/s.
- Payload Bay Demo: Aborted release of 8 simulated Starlink sats due to a stuck cargo-bay actuator.
- Failure Point: Approx. 45 minutes post-launch—a propellant leak from the main LH2 tank led to a loss of pressurization and attitude control.
Technical Deep Dive
Engine and Propellant System Analysis
SpaceX’s revised Raptor 2 engines on the Super Heavy booster and Starship upper stage ran successfully through full-duration burns. Each Raptor 2 engine provides roughly 2.3 MN thrust at sea level, with an improved high-pressure LOX-CH4 turbopump design. To mitigate earlier hardware failures, Block 2 included:
- Additional preload on main propellant-feed joints to minimize microleaks under dynamic loads.
- An enhanced nitrogen purge circuit to prevent propellant pooling in critical manifolds.
- Upgraded propellant drain valves with higher flow coefficients for faster boil-off management.
Despite these improvements, the flight encountered a new leak path in a helium pressurization line feeding the liquid methane header tank, causing tank pressure to fall below the 4.5 bar threshold for attitude-control thrusters. Without sufficient pressure, the Reaction Control System (RCS) valves could not maintain spacecraft orientation.
Structural and Thermal Protection System (TPS) Enhancements
Starship’s thermal shield on Block 2 featured 1500 ceramic–carbon composite tiles, each 20–30 mm thick, bonded to an Inconel 300 hull with variable gap fillers. Post-flight imagery—though limited by early reentry breakup—will be compared against:
- Variant A tiles with silicon-based coatings designed to reduce spallation.
- Variant B with embedded BSAS (Bonded Silicon–Aluminum–Silicate) for higher emissivity.
- New attachment pins using dual-shear Inconel fasteners to resist thermal cycling loads.
SpaceX engineers report minimal tile loss during ascent, but data from the critical reentry heating phase remains unavailable due to uncontrolled tumbling and plasma opacity.
Expert Opinions and Internal Commentary
“All evidence points to a new failure mode,” said Shana Diez, Director of Starship Engineering at SpaceX. “We’ll perform line-replacement-unit tests on the pressurization harness and revalidate on the test stand in under two weeks.”
“Breaking the streak of engine shutdowns is a major win,” said aerospace consultant Dr. Julian Mercer. “The next challenge is nailing robust pressurization and achieving a reusable thermal shield.”
Regulatory and Operational Outlook
The Federal Aviation Administration has indicated it is “actively working” with SpaceX post-flight review. While no formal mishap board has been announced, environmental permits and offshore debris-recovery plans will be scrutinized before the next orbital attempt. SpaceX aims to close out Block 2 testing within three to four flight cycles before debuting the Block 3 vehicle in late 2025.
Future Iterations and Block 3 Roadmap
Elon Musk has suggested a cadence of launches every 3–4 weeks for the next three Starships, facilitated by streamlined cryogenic proof tests—recently completed ~6 weeks prior to launch. Block 3 will introduce:
- Raptor 3 engines with upgraded ceramic bearings and additive-manufactured turbomachinery.
- An autogenous pressurization system eliminating helium in favor of hot-gas venting to reduce leak points.
- Integrated avionics upgrades to handle rapid flight computers and enhanced GNSS-aided guidance.
Conclusions
Starship’s ninth flight marked clear progress in engine reliability and booster reuse, yet underscored the criticality of pressurization integrity and TPS validation. As SpaceX pivots to fine-tune these systems, the path to full orbital flights, in-space refueling, and rapid turnaround operations remains in active development—each flight advancing the mission to Earth orbit, lunar landings, and ultimately Mars colonization.
Tags
- SpaceX
- Starship
- Raptor Engine
- Thermal Protection System
- Rocket Reusability