RoboBee Achieves Reliable Landings with Enhanced Biomechanical Landing Gear
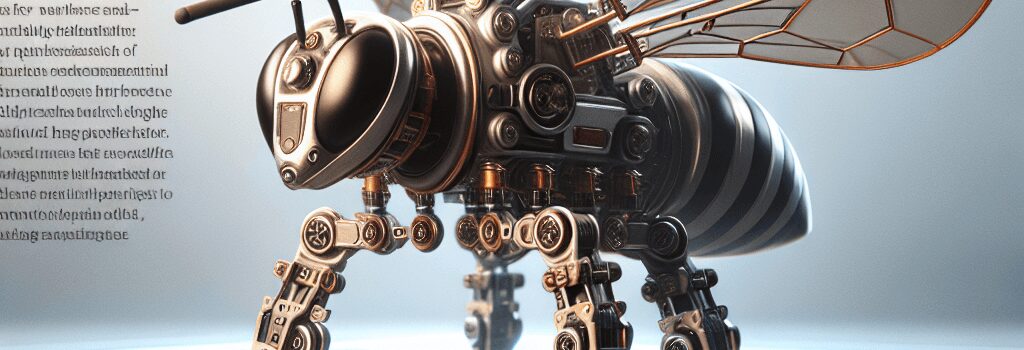
Introduction
Several years back, Robert Wood and his team at the Harvard Microrobotics Laboratory introduced RoboBee, a revolutionary insect-scale flying robot that captured the imagination of the robotics community. Originally designed to demonstrate partially untethered flight, the RoboBee has since undergone significant improvements in maneuverability, endurance, and now, landing dynamics. The latest breakthrough involves a novel landing gear architecture inspired by the crane fly’s unique jointed appendages, which enable smooth landings on uneven surfaces.
Technical Breakdown: Biomechanical Landing Gear
The new landing system leverages an underdamped spring-mass-damper model combined with viscoelastic creep properties to dissipate the energy generated upon impact. By drawing inspiration from the crane fly’s biomechanics, the research team engineered leg joints and dampers that effectively reduce the kinetic energy during landing sequences. High-speed video analysis allowed the team to observe oscillations from manually disturbed legs, capturing detailed metrics such as damping coefficients and spring constants essential for designing an optimized leg geometry.
Experimental Analysis and Methodology
- Oscillation Testing: Initial experiments involved manually disturbing the robotic leg and capturing its oscillatory behavior. The resulting data confirmed that the new joints acted much like an underdamped spring-mass system, with controlled viscoelastic creep ensuring gradual energy dispersion.
- Free-Fall Tests: Subsequent free-fall experiments utilized custom-fabricated fiberglass crash-test dummies that mimic RoboBee’s mass and inertia. High-speed cameras documented the fall, further validating the damping model with precise measurements of impact velocity and energy absorption.
- Integrated Maneuvering Sequences: The final phase of testing involved sequential takeoff, hovering, lateral transitions, and precision landings on natural plant surfaces. These trials confirmed the reliability of the landing gear under variable conditions and recapitulated real-world challenges, such as uneven terrains and multiple consecutive maneuvers.
Expert Analysis and Technical Opinions
Christian Chan, one of the graduate students on the project, remarked, “Previously, if we were to go in for a landing, we’d turn off the vehicle a little above the ground and hope for an upright, safe landing. This improvement not only minimizes the impact through aerodynamic and structural damping but sets the stage for future autonomous operations.” Experts in the field of micro-robotics are intrigued by the approach, noting that integrating such biomechanical insights can revolutionize the design of robotic landing systems at small scales. The experimental validation techniques used by the Harvard team are already influencing design protocols for other insect-scale robots.
Deeper Technical Speculations
The incorporation of underdamped models in RoboBee’s landing protocol presents interesting challenges and opportunities for further research. The fine balance between stiffness and damping in microscale components requires advanced materials with tailored viscoelastic properties. Future iterations could leverage smart materials or MEMS-based sensors integrated directly into the landing gear to enable real-time adjustments to damping parameters based on surface analytics.
Scaling Up: Future Directions and Autonomous Capabilities
Moving forward, the research is aimed at scaling up the design for larger vehicles and more complex swarms. The long-term goal is to equip RoboBee with onboard sensors and electronics that would facilitate full autonomy. By coordinating amongst a swarm of robots, these tiny flying machines could be deployed for a variety of applications including environmental monitoring, disaster surveillance, and even artificial pollination. The team is also exploring biomimetic inspirations from stingless bees and mosquitoes for further improvements in mechanical damping.
Conclusion
This recent advancement in RoboBee’s landing technology is a significant step towards eliminating the need for off-board tethered control systems—a crucial bottleneck limiting autonomous operations. As the community continues to delve into the complex interactions of aerodynamics, damped mechanical systems, and lightweight design, the potential for deploying swarms of these micro-robots in practical scenarios becomes increasingly tangible. With ongoing innovation in materials science and microelectronics, the future of RoboBee and similar insect-scale devices promises to blur the lines between biological inspiration and robotic precision.