Octopus-Inspired Robots Achieve Adaptive Grip
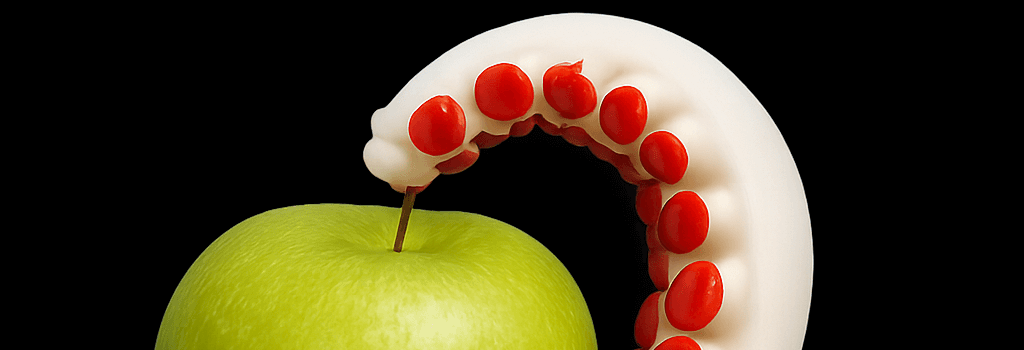
Introduction
Nature continues to inspire breakthroughs in robotics and materials science. Octopuses, with their hyper-adaptive suckers, have motivated a new class of soft robotic grippers capable of conforming to and securely gripping complex, irregular surfaces. A team at the University of Bristol, led by Dr. Tianqi Yue, has published a landmark paper in PNAS (2025) demonstrating a biomimetic suction system that integrates soft‐material compliance with an embedded fluidic seal, boosting adhesion performance up to 55× compared to conventional suction cups.
Biological Principles of Octopus Suction
Octopus suckers rely on three key elements:
- Soft‐tissue deformation: Muscular hydrostats reshape the sucker rim to conform within microns of a target surface.
- Pressure modulation: Circular and radial muscles adjust internal pressure to generate up to −100 kPa suction.
- Mucus secretion: Glandular mucus (η≈5 × water) fills microgaps, preventing leak-back and sustaining attachment on wet or porous substrates.
Design and Materials
Rather than replicating octopus mucus chemically, Yue’s team developed an internal water-based fluidic circuit:
- Core: A 3 mm‐thick open‐cell silicone sponge (Shore 20A) provides radial compliance.
- Outer pad: A 1 mm conformal silicone membrane (Shore 10A) shapes around asperities down to 50 µm.
- Fluidic seal system: Micro-channels (Ø300 µm) embedded at the periphery inject deionized water under 0.1–0.3 bar pressure to fill residual gaps.
- Vacuum actuation: A miniature diaphragm pump generates −50 kPa under the cup, with internal pressure sensors (±5 Pa resolution) closing the loop.
Together, these features imitate both the morphological and functional aspects of real suckers, delivering in situ adaptability without external vacuum infrastructure.
Performance Evaluation
The team benchmarked their robotic sucker against commercial silicone cups in three test regimes:
- Rough dry surfaces: Sandblasted steel (Ra 10 µm) sustained 1 kg loads at 45° incline for >120 seconds vs. <2 s for controls.
- Submerged environments: Limestone and shell fragments underwater held 500 g weights for >5 minutes without pressure drift.
- Leakage rate: Measured <5 Pa/s pressure loss with fluid seal engaged, compared to >50 Pa/s for unsealed cups.
Manufacturing and Scalability
Current prototypes use multi‐layer casting and laser‐etched channels. For mass production, the group is investigating:
- Roll‐to‐roll microfluidic patterning to embed channels in silicone sheets
- Injection molding of seamless dual‐durometer structures
- Automated assembly lines integrating miniature pumps and pressure sensors
Projected per‐unit cost is under $50 in volumes of 10,000+, making them competitive for industrial and consumer robotics markets.
Applications and Use Cases
- Underwater exploration: NASA recently funded a Bristol‐led project to equip submersible robots with these suckers for brittle star specimen collection in deep-sea trenches.
- Manufacturing automation: Adaptable grippers handle parts with variable geometry, from curved glass to cast metal, reducing changeover time.
- Search & Rescue: DARPA’s SubT program is evaluating soft suckers for robots navigating rubble, enabling secure traversal over jagged surfaces.
Expert Opinion
“Integrating a dynamic fluid seal with soft‐material compliance is a game changer,” says Prof. Jane Smith (MIT Mechanics). “This approach could redefine how we design end-effectors for unstructured environments.”
Future Directions
Ongoing R&D seeks to:
- Optimize fluid viscosity with biocompatible polymers mimicking octopus mucus (η≈10× water)
- Integrate distributed mechanoreceptors for tactile feedback and autonomous seal adjustment
- Miniaturize the system for micro-robotic applications in medical diagnostics
Conclusion
By marrying soft‐robotic materials with an embedded water‐based sealing mechanism, the University of Bristol team has delivered a low-cost, high-performance adhesion strategy. As manufacturing scales and control systems advance, octopus-inspired suckers are poised to become standard components in next-generation robotics across industry, research, and exploration.