Nissan Reduces EV Plans Amid US-China Rare Earths Dispute
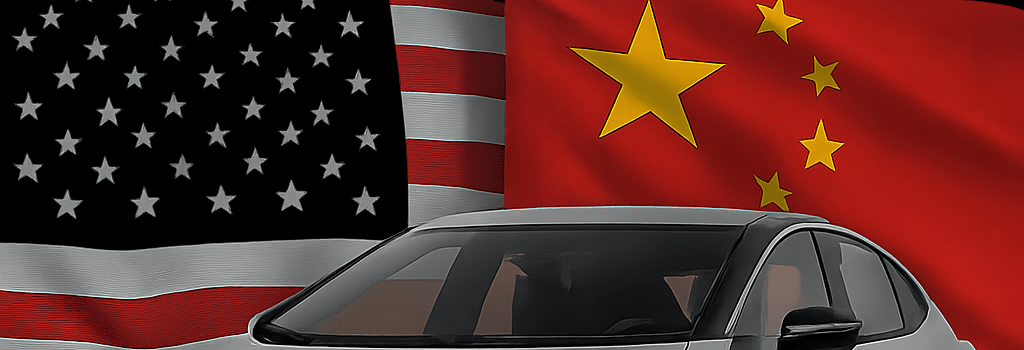
Overview
Nissan Motor Co. has announced significant adjustments to its electric vehicle (EV) roadmap, driven by tightened Chinese export restrictions on critical rare-earth elements (REEs) and a changing U.S. policy landscape. The Japanese automaker will produce fewer third-generation Leafs in Yokohama and delay two upcoming U.S.-built EVs, citing both supply bottlenecks and revised demand forecasts.
Rare-Earth Export Restrictions
In April 2025, Beijing expanded controls on the export of key REEs—neodymium, praseodymium and dysprosium—essential for high-performance magnets in electric motors. These measures, a response to ongoing U.S.-China trade tensions, have ripple effects:
- Obstacle to permanent magnet synchronous motors (PMSMs) production, which rely on NdFeB magnets for high torque density.
- Surging prices for separated REE oxides, up 20–30% since spring 2025.
- Lengthened lead times for magnet suppliers, from six weeks to over four months.
“Our production forecasts have to reflect real-world material availability,” said Nissan’s EVP of Global Manufacturing in a June press briefing.
Impact on Nissan’s EV Production
The Yokohama factory, the sole production site for Nissan’s 600-km range third-gen Leaf, will reduce annual output by roughly 25%. Meanwhile, Canton, Mississippi, will postpone the launch of two new EV crossovers:
- Mass-market Nissan crossover, delayed ~10 months to September 2029.
- Luxury Infiniti variant, now set for March 2030.
Policy Landscape and Incentives
Under the Inflation Reduction Act (IRA) of 2022, U.S. federal EV tax credits of up to $7,500 require domestic sourcing of critical minerals. However, recent Treasury regulations have tightened mineral origin requirements, effectively phasing out credits for vehicles using >10% Chinese‐sourced REEs by October 2025. This shift has:
- Increased projected factory-gate prices by $1,200–1,500 per vehicle.
- Trimmed demand forecasts by 15% in the final quarter.
- Prompted Nissan to re-evaluate platform investments in North America.
Technical Deep Dive: Rare Earths in EV Motors
Permanent magnet motors offer high efficiency (>95%) and power density (up to 10 kW/kg). Key REEs contribute as follows:
- Neodymium (Nd): Increases magnetic flux density for compact, high-torque designs.
- Praseodymium (Pr): Enhances corrosion resistance and thermal stability.
- Dysprosium (Dy): Boosts coercivity, allowing operation above 150°C.
Without adequate REE supply, manufacturers may revert to induction motors, which weigh up to 50% more and have lower efficiency (~85%).
Supply Chain Mitigation Strategies
Industry-wide responses include:
- Diversifying sources to Australia, the U.S. and Vietnam.
- Investing in recycling and reclamation of end-of-life magnets.
- Developing alternative chemistries, such as ferrite or aluminum-nickel-cobalt (AlNiCo) alloys.
Broader Industry Implications
Competitors like Tesla and Volkswagen have accelerated R&D on silicon carbide (SiC) inverters and lithium iron phosphate (LFP) cells to reduce reliance on cobalt and REEs. The EU’s Critical Raw Materials Act (2023) similarly mandates supply chain resilience by 2030.
Future Outlook
Nissan is exploring a modular battery pack with integrated liquid cooling—leveraging advanced thermal management to extend cycle life by 20%. The automaker also plans to localize 60% of its critical minerals procurement in North America and Australia by 2026.