NASA Swaps Artemis II Engine Amid Pre-Launch Checks
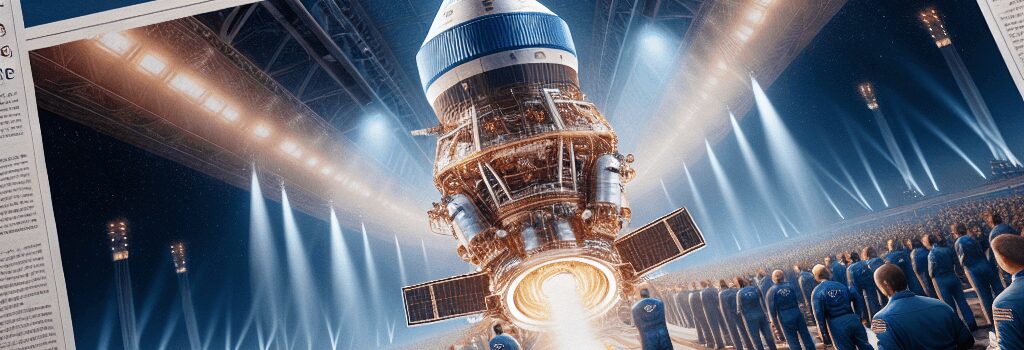
Introduction
Technicians at NASA’s Kennedy Space Center (KSC) recently removed RS-25 engine E2063 from the core stage of the Artemis II Space Launch System (SLS) after detecting a hydraulic leak in the main oxidizer valve actuator. In its place they installed E2061—an engine nearly twice as old—underscoring both the flexibility of ground support operations and the tight inventory of heritage hardware remaining from the Space Shuttle era.
Hydraulic Leak Discovery and Valve Actuator Details
During routine pre-flight checkout last month, pressure transducers on the engine’s liquid oxygen (LOX) feed line registered anomalies in the actuator control loop. The main oxidizer valve actuator, a hydraulic servo mechanism that meters LOX at cryogenic temperatures (~20 K), exhibited a micro-leak at the high-pressure sleeve seal. Left unchecked, even minute leaks can introduce cavitation into the turbopump inlet and trigger unwanted pressure spikes (up to 3,100 psi in the combustion chamber), risking engine performance or shutdown.
- Actuator pressure: 5,000 psi hydraulic fluid
- Valve orifice diameter: 1.7 inches
- Sensing accuracy: ±0.2 bar
Vertical Replacement Operations at the Vehicle Assembly Building
Remarkably, engineers performed the swap while the 212-foot-tall core stage stood vertical on the mobile launch platform inside VAB High Bay 3. Using NASA’s 30×30 ft vertical engine installer—a dedicated ground support fixture designed during SLS development—they disengaged 50,000 mechanical and electrical connections in under 48 hours. The entire operation involved:
- Powering down hydraulics and purging LOX plumbing
- Unbolting the nine 75-mm titanium engine mounts
- Lowering the faulty unit on a cryo-compatible tooling cradle
- Reinstating E2061 and re-pressurizing feedlines
Engine Specifications and Service History
The RS-25 remains one of the highest-performing hydrolox engines ever built:
- Thrust (vacuum): 512,000 lbf
- Specific impulse: 452 s (vacuum), 366 s (sea level)
- LOX flow rate: 1,030 lb/s
- LH₂ flow rate: 1,830 lb/s
- Max chamber pressure: 3,090 psi
Engine E2063 was built in 2015 at Stennis Space Center using surplus shuttle turbopumps and never flew. Its replacement, E2061, dates to 2008, flew twice on STS-133 and STS-134, and has since been refurbished and recertified under NASA’s Shuttle-to-SLS conversion program.
Engine Health Monitoring and Leak Mitigation
To reduce unscheduled removals, NASA is expanding its real-time health monitoring suite. On Artemis II, data from high-fidelity fiber-optic temperature sensors, ultrasonic acoustic detectors, and redundant pressure transducers feed into an onboard analytics package. According to RS-25 lead engineer Dr. Maria Gonzales, “These systems allow us to detect seal erosion down to sub-millimeter tolerances, giving us confidence in engine reusability metrics and safety margins.” Future upgrades may incorporate machine-learning models to predict seal fatigue based on historical flight and test-stand data.
Comparative Analysis: RS-25 vs. Next-Generation Methalox Engines
While the RS-25 excels in performance, new entrants like Blue Origin’s BE-3U and SpaceX’s Raptor declare higher thrust-to-weight and lower per-flight costs through methane fuel. A brief comparison:
- RS-25: 1,150 sec Isp (vacuum), mature design, $100 M per new unit
- BE-3U: 460 sec Isp, simplified cycle, reusable, ~$30 M per engine
- Raptor: 380 sec Isp, full-flow staged combustion, methane-powered, <$10 M per engine
Though RS-25s are legacy hardware discarded after each SLS flight, commercial methalox engines promise rapid turnarounds and lower fixed costs—factors driving debates in Congress over sustainable deep-space infrastructure.
Program Sustainability and Budget Implications
NASA’s Inspector General estimated in 2023 that new RS-25 engines would cost $100 million apiece and contribute to an SLS launch price of ~$2.5 billion. Even with continuing resolutions securing funding for Artemis IV, further flights hinge on Congressional appropriations. The agency is evaluating a larger, more powerful Exploration Upper Stage (EUS), budgeted at $5.7 billion, but faces pressure to pivot toward lower-cost commercial vehicles for Mars missions.
“Every unplanned engine swap underscores the need for cost-effective alternatives,” says aerospace analyst Karen Matthews of the Center for Space Policy. “Balancing performance with fiscal responsibility will shape America’s path beyond lunar orbit.”
Looking Ahead
With E2061 now operational in Engine 4 position, Artemis II remains on track for early 2026, weather and Orion spacecraft readiness permitting. Meanwhile, test firings of the first new block II RS-25 (E2163) at Stennis have achieved full-duration burns, validating upgrades to the powerhead and seals ahead of the Artemis V backup mission.
As NASA refines its engine inventory and explores commercial partnerships, the Artemis program’s success will depend on integrating heritage hardware with next-generation propulsion to deliver sustainable, affordable human exploration of deep space.