GM’s LMR Battery Boosts Range and Cuts Costs
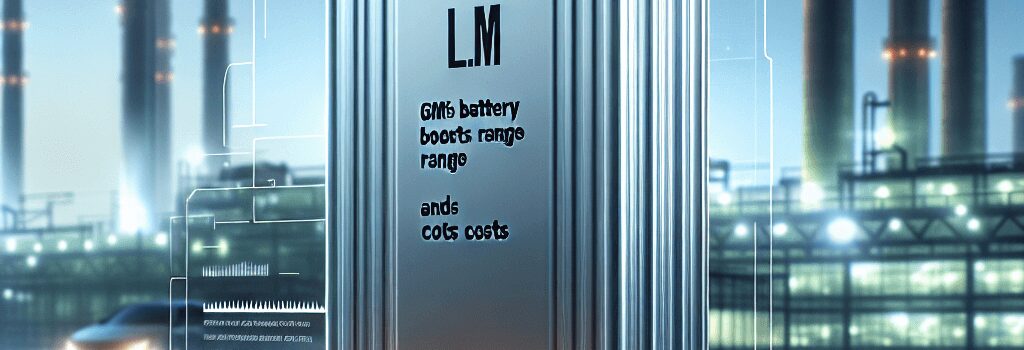
Introduction
General Motors is preparing to launch its next-generation lithium‐manganese‐rich (LMR) battery chemistry in 2028, promising up to 30% more range than current lithium iron phosphate (LFP) cells at near‐LFP price points. Developed in partnership with LG Energy Solution and prototyped through more than 300 full-size cells, LMR technology reduces cobalt content by over 60%, cutting both cost and weight while preserving energy density close to nickel manganese cobalt (NMC) levels.
Why LMR Matters
- Cost Reduction: By displacing expensive cobalt with manganese, GM targets pack-level costs near $100/kWh—comparable to LFP—while delivering energy densities above 220 Wh/kg.
- Weight Savings: Lower cobalt content trims pack weight by up to 12 kg in full-size pickups like the Silverado EV, improving efficiency and payload capacity.
- Range Improvement: LMR-equipped trucks will achieve ~350 miles (560 km) per charge, bridging the gap between entry-level LFP (~250 miles) and long-range NMC (~400 miles).
Technical Deep Dive: Electrode Chemistry and Materials Sourcing
The LMR cathode formula shifts the NMC ratio from 80/10/10 (Ni/Mn/Co) to approximately 50/45/5, stabilizing high-voltage performance with a manganese-rich spinel phase. Key innovations include nano‐coating the cathode particles with a lithium phosphate layer to suppress manganese dissolution at elevated voltages (4.3 V). On the anode side, graphite blended with 5% silicon enables higher reversible capacity (~450 mAh/g focus) without compromising cycle life.
GM’s strategic investment in Element 25’s Louisiana facility secures a domestic supply of battery-grade manganese sulfate for up to one million packs per year. This vertically integrated approach reduces ocean freight costs by over 15% and slashes lead time for quality control issues from eight weeks to under two.
Supply Chain Resilience and Onshoring Benefits
Kurt Kelty, GM’s vice president of battery systems after 12 years at Tesla, emphasizes the importance of localizing raw‐material processing and cell assembly. “Shortening our supply chain not only lowers costs but dramatically improves defect containment and recycling throughput,” Kelty says. He highlights GM’s new Wallace Battery Cell Innovation Center in Warren, Michigan, where production-speed pilot lines accelerate cell validation under extreme conditions—from –30 °C cold‐soak to 60 °C thermal cycling.
In collaboration with Redwood Materials, GM is scaling up black‐mass recycling of end‐of‐life cells to recover cobalt, nickel, and manganese with 95% material yield, further shrinking the net material cost per kWh by up to 10% over the next five years.
Comparative Analysis: LMR vs. LFP vs. NMC
Chemistry | Energy Density | Cobalt Content | Cost ($/kWh) | Range (Full‐Size Truck) |
---|---|---|---|---|
LFP | 140–160 Wh/kg | 0% | 90–100 | 250 miles |
LMR (GM, 2028) | 210–230 Wh/kg | 5% | 100–110 | 350 miles |
NMC 811 | 240–260 Wh/kg | 10–15% | 115–125 | 400 miles |
Expert Opinions and Industry Context
Automotive analyst Dr. Sarah Lee of GreenVolt Consulting notes, “GM’s LMR approach is a pragmatic trade-off—retaining high energy density while driving down reliance on conflict minerals. It aligns with broader industry trends at Ford and CATL toward manganese‐rich cathodes.” Ford recently announced its own low‐cobalt manganese formulation, set to debut in late-2029, confirming that LMR‐type chemistries are becoming mainstream.
Meanwhile, battery startups such as Our Next Energy (ONE) and startup 24M are exploring semi-solid electrodes and anode‐free designs to push energy densities beyond 350 Wh/kg, but GM’s bet on incremental improvements promises faster time-to-market on validated production lines.
Future Outlook and Roadmap
- 2026: Pilot production of LMR cells at 100 MWh/year scale in Warren, MI.
- 2028: Launch of LMR in Silverado EV and GMC Hummer EV chassis with six large-format prismatic cells per pack.
- 2030+ Integration of next-gen silicon‐enriched anodes and solid‐state separators to boost cycle life to 2,500+ cycles.
Kelty has also teased “advanced electrolyte additives” designed to maintain fast-charge capability in sub-zero temperatures, addressing one of the last remaining barriers to consumer EV adoption in cold climates.
Conclusion
With LMR, GM aims to achieve price parity with internal combustion engine vehicles, a $7,500 gap currently offset only by federal tax credits. If successful, LMR will set a new standard for affordable, long-range EVs built largely from domestically sourced materials. As LMR rolls out alongside existing LFP and NMC offerings, GM is positioning itself at the forefront of battery innovation—delivering on the promise of widespread, cost-competitive electrification.