Brembo’s Brake Factory: Tech Innovations in Next-Gen Braking Systems
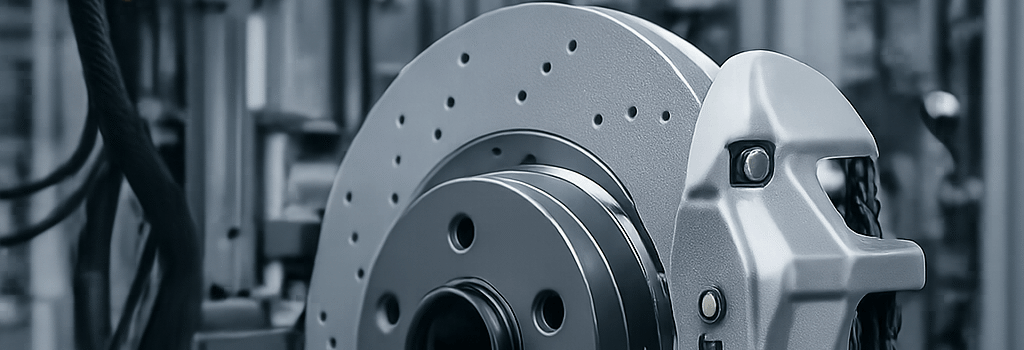
Le Mans at Night: The Ultimate Brake Test Bench
It’s 2 a.m. at the Circuit de la Sarthe, and the 24 Hours of Le Mans is roaring past its midpoint. Fans cluster around Turn Four, umbrellas in hand, eyes fixed on a procession of hypercars. But the real spectacle isn’t the drone shows or pitlane lights—it’s the glowing brake calipers of the Cadillac V-Series.R and its rivals. Brembo’s carbon composite discs heat from 300 °C to over 815 °C in seconds, enduring more than 4,000 high-energy deceleration events over 24 hours without replacement.
The Heart of Brembo in Bergamo
Founded in 1961, Brembo’s R&D and manufacturing campus sits within the Kilometro Rosso innovation district. The facility spans 80,000 square meters and houses research labs, digital twins, and production cells. Early partnerships with Alfa Romeo and Ferrari forged Brembo’s reputation—today every car on the 2025 Le Mans grid uses at least one Brembo component, from cast-iron rotors to titanium caliper pistons.
Carbon Composite Brake Discs
- Outer diameter up to 398 mm, thickness 34 mm, tolerance ±0.05 mm
- Carbon fiber reinforced carbon (CFC) laminated in 50 layers, autoclave cured at 120 bar and 1,000 °C
- Laser-drilled 1.5 mm holes, 2 mm pitch for thermal regulation and dust evacuation
“Our discs must handle surface temperatures above 1,000 °C without microcracking,” says Dr. Laura Smith, composite materials expert at Politecnico di Milano.
Cast-Iron and Ceramic Options
For production cars Brembo offers nodular cast-iron rotors with vaned internal channels. Thermal conductivity exceeds 50 W/mK, enabling rapid cooldown. Carbon-ceramic discs combine silicon carbide matrix and carbon filaments, reducing unsprung mass by up to 30 percent.
From Machining to Mechatronics: Brembo’s Smart Factory
Brembo has invested over €200 million in Industry 4.0 upgrades. Five-axis machining centers robotically rough-cut rotors, then finish at 0.01-mm precision. Each machining cell is linked to a digital twin, simulating thermal loads via finite element analysis before the first cut.
Automated Inspection and Quality Control
- Laser profilometers scan surfaces at 5 µm resolution
- Inline ultrasonic sensors detect porosities in ceramic substrates
- Automated deburring and cleaning with HEPA-filtered vacuum stations
Sensify: The Next Evolution in Braking Technology
In 2024 Brembo launched Sensify, a software-defined, fluid-free brake system. Unlike legacy brake-by-wire, Sensify integrates hydraulic actuators, electric motors, and a real-time control unit running a 1,000 Hz loop. Onboard sensors include 6-axis accelerometers, strain gauges, and pressure transducers. An LSTM-based AI model predicts pad wear and adjusts distribution per wheel in under 2 ms.
“Sensify transforms braking into a mechatronic platform, blending mechanical engineering with AI,” explains CEO Daniele Schillaci.
Integration with Electric Vehicles and Regenerative Braking
As automakers shift to electrification, braking systems must cooperate with regenerative braking modules. Brembo’s EV kit includes an electric brake booster that modulates pressure between hydraulic circuits and regenerative torque, optimizing energy recapture without compromising pedal feel. Tests on a prototype EV SUV achieved a 20 percent increase in energy recuperation.
Expert Opinion: Bridging Traditional and Software
Mark Johnson, senior systems engineer at a leading EV startup, notes:
“Combining Sensify’s data analytics with vehicle control units allows predictive maintenance and real-time fault detection, essential for autonomous fleets.”
Future Outlook: Autonomous and AI-Driven Braking
Brembo plans to integrate vehicle-to-cloud connectivity, feeding anonymized braking data into a central AI that refines algorithms across the fleet. By 2027, Brembo aims to deploy self-calibrating brake systems that adjust for pad geometry, rotor warp, and road conditions without human intervention.
Conclusion
Brembo’s evolution from cast-iron foundry to Industry 4.0 powerhouse illustrates how software, AI, and advanced materials converge to redefine automotive safety and performance. As racing disciplines and electric mobility reshape demands, Brembo remains at the forefront, turning red-hot calipers into data-rich, intelligent systems.