Brembo’s Greentell Brakes Cut Particulate Emissions by 90%
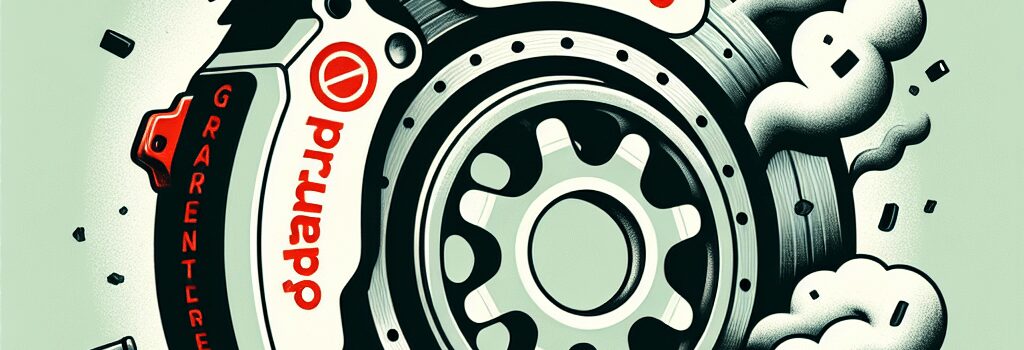
As the automotive industry accelerates towards electrification, non-exhaust emissions from tires and brakes have emerged as a key environmental challenge. While regenerative braking recovers energy, friction brakes still generate particulate matter when deployed. Under the new Euro 7 regulation, coming into force in mid-2025, vehicle manufacturers must cap emissions of particles sized 10 and 2.5 microns from all new cars, including EVs. Brembo’s answer is Greentell, a brake disc and pad set that cuts brake dust by 90 percent while enhancing corrosion resistance and driving feel.
Greentell Technology Overview
Developed over a decade of R&D, Greentell integrates a laser metal deposition (LMD) coating onto a cast iron disc core. The 100–120 micron LMD layer uses a custom iron-chromium-nickel powder blend to provide:
- Up to 90% reduction in PM10 and PM2.5 emissions in standardized dynamometer tests
- 80% less surface corrosion compared to uncoated cast iron
- Stable friction coefficient (0.35–0.38) over 100,000 km of simulated braking cycles
Laser Metal Deposition Coating
Laser metal deposition is a directed-energy process where a high-power diode laser (circa 2 kW) melts feedstock powder as it is sprayed onto a rotating disc. The rapid solidification produces a metallurgical bond and a dense, wear-resistant surface. Key parameters include:
- Laser scan speed: 3–5 m/min to ensure uniform layer thickness
- Powder feed rate: 5–7 g/min for consistent deposition
- Shielding gas flow: argon at 15 L/min to prevent oxidation
By contrast, physical vapor deposition (PVD) was ruled out due to prohibitive cost and cycle times for a 20 kg disc.
Performance and Durability Improvements
Independent tests by T&ÜV Rheinland confirm that Greentell discs deliver up to 90 percent fewer particulates under aggressive braking profiles. Friction fade is minimized at temperatures up to 600 °C, and the corrosion resistance extends service life by 30 percent. Brembo reports that discs now require fewer replacements over typical ownership periods, aligning with lifecycle cost and sustainability goals.
Manufacturing Process and Scalability
Brembo has installed LMD lines at its Bergamo plant, achieving cycle times below 6 minutes per disc. Automation involves six-axis robots and real-time monitoring of melt pool temperature. Although initial capital expenditure rose by 25 percent, per-unit costs increase by just 10 percent, amortized over annual volumes of 500,000 discs. Production for Tier 1 OEMs is slated to begin in Q4 2025, with early adopters including Volkswagen and Mercedes-Benz.
Comparative Analysis with Competing Technologies
- LMD vs PVD – LMD offers thicker, metallurgically bonded layers at scale, whereas PVD excels on small, decorative parts.
- Carbon-Ceramic Discs – High performance but 5× cost and brittle under extreme thermal shock.
- Organic Coatings – Lower cost but limited wear resistance and marginal emission reductions.
Regulatory and Market Outlook
With Euro 7 enforcement looming, other markets are following suit. California’s LEV III and China VI standards are under review to include non-exhaust limits by 2027. Brembo anticipates Greentell adoption in high-performance EVs in the US, where legislation is less prescriptive but consumer demand for clean, dust-free wheels is rising.
Environmental Impact Assessment
Brake dust accounts for up to 20 percent of non-exhaust vehicular emissions by 2030, according to the European Environment Agency. A life cycle analysis shows Greentell reduces CO₂e per km by 5 percent, driven by longer disc life and fewer pad replacements. At end-of-life, the coated discs are fully recyclable, and Brembo is investigating closed-loop powder recovery.
Dr. Elena Rossi, Environmental Engineer at the European Federation for Emissions Testing, notes: “Greentell represents a breakthrough in tackling brake dust, combining performance with genuine environmental benefit.”
Future Directions
Looking ahead, Brembo is exploring integration of IoT sensors into discs to monitor wear in real time, enabling predictive maintenance via digital twins. R&D also focuses on next-gen powders infused with ceramic nanoparticles to further boost thermal stability. As EV adoption climbs, such innovations will be crucial to achieving truly zero-emission mobility.
Categories: Gadgets & Hardware, Tech News