Baxter: Trump Tariffs to Cost $60–70 Million in 2025
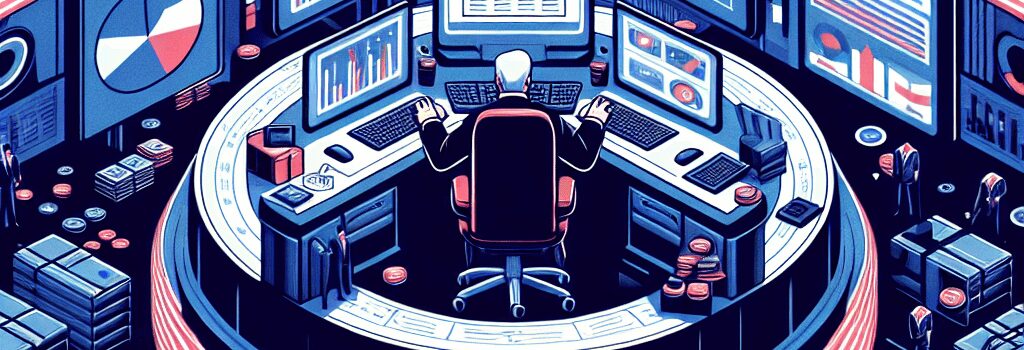
During its Q2 earnings call on May 1, 2025, Baxter International’s Executive Vice President and CFO Joel Grade disclosed that U.S. import duties stemming from the Trump administration’s tariff regime are expected to increase the company’s costs by $60 million to $70 million this calendar year. This announcement underscores the growing pressure on hospitals, clinics, and pharmaceutical distributors already grappling with lean inventories and supply‐chain disruptions.
Background on U.S.–China Tariffs and the Medical Supply Chain
Since 2018, the United States and China have imposed successive rounds of reciprocal tariffs on hundreds of billions of dollars of goods. Although many Baxter products are U.S.-manufactured from domestic components, the company still sources key raw materials and subassemblies—such as sterile tubing, polyvinyl chloride (PVC) resin for IV bags, and saline concentrate—from Asia, Europe, and Latin America. According to industry trade group Advanced Medical Technology Association (AdvaMed), medical devices account for nearly 4% of U.S. imports from China, translating into tens of millions in added duties each year.
Financial Impact on Baxter International
- Tariff-Related Expense: An estimated $60 M–$70 M added COGS (cost of goods sold) in 2025, ~0.6% of annual revenue.
- Geographic Exposure: Less than 10% of Baxter’s global sales derive from China, but high‐tariff rates (up to 25%) amplify the cost impact.
- Key Product Lines Affected: IV fluid bags (PVC-based), prefilled syringes, peritoneal dialysis cyclers, and certain infusion pumps.
Technical Overview of Affected Products
Many of Baxter’s flagship devices rely on precision polymer components and single‐use disposable sets. For example:
- PVC Resin for IV Bags: Requires medical-grade, DEHP-free formulations to maintain biocompatibility and chemical stability. Tariffs on resin additives and extrusion lines feed directly into bag cost.
- Infusion Pumps: Incorporate microprocessor boards, stepper motors, and silicone tubing—key subcomponents that are often sourced from specialized contract manufacturers in Asia.
- Sterilization Supplies: Gamma-irradiation packaging and ethylene oxide sterilization services also face indirect cost increases via tariff‐driven supply‐chain inflation.
Mitigation Strategies and Operational Adjustments
Baxter is deploying a multi-pronged approach to dampen the tariff headwind:
- Inventory Pre-Buy: Stockpiling critical raw materials ahead of anticipated tariff hikes to lock in lower landed costs.
- Supplier Diversification: Qualifying alternative vendors in Mexico and Eastern Europe to shift volumes away from high-tariff origins.
- Logistics Optimization: Exploring transshipment via Canada to leverage lower duty rates under USMCA, and rerouting shipments through non-tariffed countries.
- Pricing Adjustments: Implementing targeted price increases for certain product lines, subject to hospital budget constraints and contract terms.
- Trade Lobbying: Working with AdvaMed and the U.S. Chamber of Commerce to seek tariff exemptions for critical medical components and outbreak-response devices.
Expert Analysis and Industry Outlook
“This isn’t just a balance-sheet problem,” says Dr. Allison Chen, a supply-chain consultant at McKinsey & Company. “When medical suppliers like Baxter absorb extra tariff costs, we risk passing those costs — and potential shortages — onto patients.” A recent study by the Duke Global Health Innovation Center warns that hospitals operating with less than 30 days of critical supplies are one major manufacturing incident—or one additional tariff round—away from elective procedure postponements.
Policy Developments and Future Outlook
As of June 2024, the Biden administration initiated a review of Section 301 tariffs on medical goods, with the International Trade Commission (ITC) expected to deliver recommendations by Q3 2025. Meanwhile, congressional proposals such as the Medical Supply Chain Resiliency Act seek to incentivize domestic polymer and device manufacturing via tax credits and grants. Should these measures pass, companies like Baxter could eventually see relief from both tariffs and long‐term supply vulnerabilities.
Conclusion
Baxter’s forecasted $60 M–$70 M tariff burden highlights a broader challenge for the U.S. health care sector: balancing global sourcing efficiencies against national economic policy shifts. As industry stakeholders await potential tariff rollbacks or exemptions, many have already begun fortifying their supply chains through onshoring, nearshoring, and strategic inventory management.