Four-Wheel Steering: Trucks to AI-Driven Steer-by-Wire
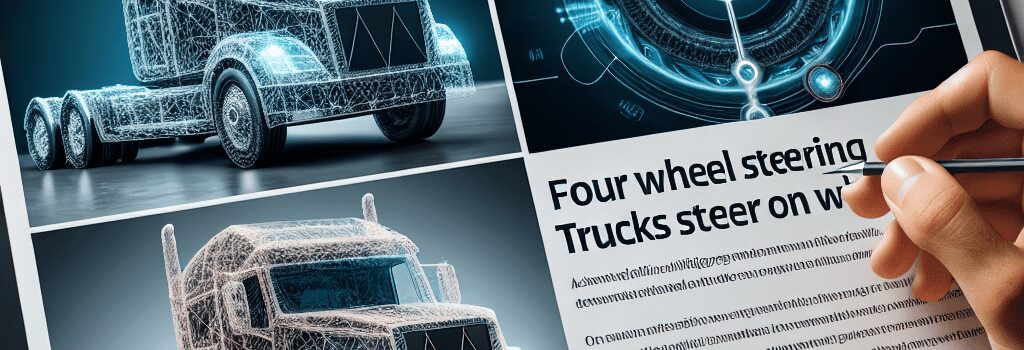
Introduction
Four-wheel steering (4WS) remains one of the most elegant yet underappreciated advances in vehicle dynamics. By actively steering both the front and rear axles, 4WS systems deliver a blend of low-speed maneuverability and high-speed stability unmatched by conventional two-wheel steer architectures. In this deep dive, we trace 4WS from its experimental origins in the early 20th century through its heyday in 1980s Japanese sport coupes, to the latest electric trucks, luxury sedans, and emerging steer-by-wire implementations driven by AI and advanced sensor fusion.
Historical Development of Four-Wheel Steering
The concept dates back to pre-World War I era American ¾-ton to 10-ton trucks such as the Cotta Cottamobile and Jeffery/Nash Quad lorry, which used mechanical linkages to improve off-road turn-in. These early 4WS rigs featured rudimentary yokes and tie rods that shifted both axles in unison or slight offsets under heavy steering loads.
- 1907–1915: Experimental 4WS in military and agricultural trucks, mechanical bevel-gear linkages.
- 1950s–1970s: Low-volume industrial vehicles and mining rigs adopted simple rear-axle steering for tight aisles.
- 1983: Mazda MX-02 concept showcased a hydraulic-assisted 4WS in a passenger car format.
Mechanical vs. Hydraulic 4WS in the 1980s–’90s
Honda’s 1988 Prelude Si was the first mass-production passenger car to offer an active, entirely mechanical four-wheel steering option. A torque-sensing shaft linked the front rack to a planetary gearset in the rear, producing:
- Same-phase: Up to 1.5° rear steering at low front-rack angles for marginal high-speed stability improvements.
- Opposite-phase: Up to 5.3° rear steering at high steering-wheel angles, shrinking the turning circle by ~10%.
Nissan’s HICAS (“High Capacity Actively Controlled Steering”) followed in 1989, using a dedicated ECU and hydraulic actuator on the rear subframe. Depending on vehicle speed and yaw‐rate, HICAS would apply ±1° toe adjustments to refine slalom times by up to 0.2 sec and improve lane-change responses by 15%.
Mazda (1988 626 Turbo) and Mitsubishi (1987 Galant VR-4) offered hybrid systems that combined same-phase steering above 50 km/h with limited geometry changes at low speed. Yet complex packaging, rising Yen-dollar exchange rates, and steep MSRP premiums (often +$2,000–$5,000) curtailed widespread adoption.
Modern Implementations in Electric Pickup Trucks
In 2002 GM introduced Quadrasteer on the Chevrolet Silverado and GMC Sierra HD lines, using a rear rack-and-pinion driven by an electric motor to deliver 15° opposite-phase steering below 72 km/h and 5° same-phase above. Benefits included:
- Turning circle reduced from 14.3 m to 11.3 m (22% tighter).
- Enhanced trailer tracking with a special towing mode limiting rear wheel deviation to 12°.
- Improved lane-change stability under 3,000 kg tow loads.
However, the $5,600 option and concerns over long-term durability in work applications led to its demise by 2006.
Fast-forward to 2025: the GMC Sierra EV and Hummer EV resurrect 4WS with fully sealed electric actuators, integrated temperature management, and over-the-air control-map updates. These modern systems leverage:
- Drive-by-wire front and rear actuators delivering ±10° steering with 0.1° resolution.
- YAW-rate, lateral-acceleration, and steering-torque sensors sampling at 1 kHz for predictive control loops.
- Domain-controller architecture enabling fail-safe modes and redundancy for SAE Level 2+ ADAS functions.
Steer-by-Wire and AI-Enhanced Control
Moving beyond mechanical linkages, multiple OEMs and Tier 1s (ZF, Continental) are prototyping full steer-by-wire systems. Infiniti’s upcoming QX50 flagship offers a steer-by-wire rear axle, while Cadillac’s Celestiq concept and Toyota’s Lexus RZ 450e demonstrate single-wire front and rear control:
- Elimination of the intermediate steering column lowers fix-it complexity and reduces cabin intrusion.
- AI-driven algorithms adjust front/rear phasing in real-time based on driver behavior, road curvature, and friction estimates from predictive vision processing.
- Hardware-in-the-loop (HiL) testing leverages digital twins to certify stability under all permutations of speed, load, and tire wear.
Technical Specifications and System Architecture
Typical modern 4WS architectures comprise:
- Rear Actuator: Brushless DC motor (4–8 Nm continuous torque) with planetary gearbox and high-precision absolute encoder.
- Control Unit: ARM Cortex-R based ECU sampling sensors at 1 kHz, running a dual‐core HRTOS for yaw and lateral control.
- Sensors: 3-axis gyros, accelerometers, torque sensors, wheel-speed sensors, optical curvature cameras.
- Communication: Automotive Ethernet (100 Mbps) or CAN FD (up to 8 Mbps) with redundant links for ISO 26262 ASIL D compliance.
Expert Opinions and Industry Outlook
“Four-wheel steering is no longer a niche — it’s becoming a prerequisite for high-performance EVs and luxury SUVs,” says Dr. Karin Müller, head of Vehicle Dynamics at ZF. “New materials and compact actuators have cut weight by 30%, and advanced software now integrates seamlessly with torque vectoring and ADAS.”
According to a 2024 study by AutoTech Consulting, 4WS penetration in the premium EV segment is projected to grow from 8% in 2023 to 24% by 2028, driven by consumer demand for improved low-speed parking and high-speed lane change stability.
Future Directions & Autonomous Integration
As vehicles approach SAE Level 4 autonomy, 4WS will be critical for:
- Urban Shuttles: Tight maneuvers in congested environments, achieving up to 40% tighter turning radii.
- Last-Mile Delivery Robots: Small-scale 4WS platforms reduce curb-to-curb transit footprints by 15%.
- Redundant Safety: Dual actuators per rear wheel enable continued operation under single-point failures, essential for passenger safety.
Conclusion
From the rugged pioneer trucks of the early 1900s to today’s AI-driven steer-by-wire EVs, four-wheel steering has come full circle. Its core promise — tighter low-speed handling paired with rock-solid high-speed stability — remains as compelling now as when Honda and Nissan first enthralled journalists three decades ago. With ongoing advances in control algorithms, sensor fusion, and actuator miniaturization, 4WS is poised to become a mainstream feature, not just on luxury cars, but on the next generation of autonomous, urban, and commercial vehicles.