GM’s Use of AI and Tech in Motorsports
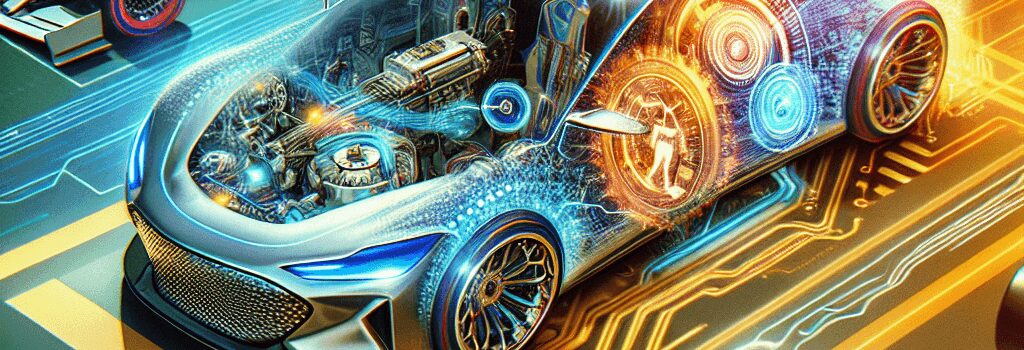
General Motors’ newly unveiled Charlotte Technical Center is poised to become the beating heart of the automaker’s global racing efforts—from NASCAR ovals to the paddock at Spa-Francorchamps and, soon, the F1 grid. Beyond the roar of engines and checkered flags, GM engineers are using cutting-edge simulation, electrified powertrains, and artificial-intelligence-driven analytics to refine vehicle dynamics, accelerate software development, and train the next generation of performance engineers.
State-of-the-Art Charlotte Technical Center
Located in Concord, North Carolina, GM’s 130,000 sq ft motorsport hub combines traditional workshops with advanced labs:
- Driver-in-the-Loop Simulators: Six 6-DOF motion platforms running real-time physics at 8 kHz, paired with 270° field-of-view LED screens and industry-standard software (e.g., SCANeR, rFpro) for tire, aero, and powertrain emulation.
- Shaker and Vibration Rigs: Systems capable of 16,000 lbf in random and sine sweep modes, forcing component and chassis fatigue life testing under race-level loads.
- Driver Performance Gym: VO₂ max treadmills, inertial measurement units (IMUs) for neuromuscular training, hot-and-cold environmental chambers to simulate extreme cockpit conditions.
- Rapid Prototyping Suite: Multi-material 3D printers (SLS, SLA, carbon-fiber composite) and CNC cells for next-day brackets, ductwork, and even brake caliper mockups.
Remote Race Command and Data Analytics
GM’s racing command centers are conference rooms lined with 4K and 8K screens displaying live telemetry, video streams, and AI-driven insights. Key technologies include:
- Edge Compute Nodes: Ruggedized servers in pit lane communicating over private 5G and microwave links to AWS EC2 C6gn instances for rapid data offload and post-session batch processing.
- AI Caution Prediction: Natural language processing on radio feeds combined with track-embedded DRS sensors yielding 92% accuracy in predicting yellow flags up to 30 seconds in advance.
- Image-Based Damage Detection: Convolutional neural networks analyzing 60 fps broadcast and photographer shots—alerting engineers to suspension or bodywork breaches within two seconds.
- Accelerated CFD Workflows: ANSYS Fluent meshes of 15 million cells run on NVIDIA A100 GPUs, cutting simulation turnaround from four weeks to under four hours for a full aero development cycle.
Vehicle Dynamics and Engineering Development
Senior Vice President Ken Morris emphasizes that real-world racing hones skills impossible to simulate in isolation. Key areas of focus:
- Torsional Stiffness Tuning: Chassis targets of 18 kN/deg achieved via optimized roll-bar geometry and carbon-fiber cross-bracing, improving cornering precision and feedback.
- Suspension Kinematics: Multi-link rear end with pushrod-activated dampers offering independent control of camber and toe under lateral load.
- Brake Thermal Management: CFD-designed ductwork with variable‐geometry flaps directing air to 6-piston monobloc calipers, maintaining rotor surface temperatures around 550 °C during endurance stints.
Electrification Roadmap and BEV NASCAR Feasibility
Hybrid powertrains have been mandatory in F1 since 2014, and GM’s endurance programs now deploy compact supercapacitor units in IMSA and WEC machines. Looking at an all-electric NASCAR series, GM engineers cite several challenges and development paths:
- Battery Architecture: 700 V NMC-811 pouch cells achieving 260 Wh/kg, liquid cooling with microchannel heat exchangers able to dissipate 250 kW of continuous thermal load.
- Regeneration Limits: Oval circuits offer negligible regen opportunities; engineers are exploring brake blending strategies and kinetic energy recovery during pit entries.
- Prototype BEV Support Series: A 2026 concept car featuring an 800 V silicon carbide (SiC) inverter capable of peak power delivery of 600 kW, targeting a 1.9 second 0-60 mph time and a 300 mi range in mixed-use race conditions.
“For electric powertrains, the development-iteration cycle of racing—run, data analysis, software update, repeat—is crucial,” Morris notes. “We hire battery and drive-unit engineers who want direct transfer to production EVs, from cell chemistry to traction-inverter calibration.”
Cloud-Connected Simulation and Data Analytics
Beyond on-site compute, GM is integrating cloud-native pipelines:
- High-Performance HPC Integration: Microsoft Azure HBv3 clusters for large‐scale finite‐element analysis and multi‐body dynamics simulations, slashing design loop times by 60%.
- Digital Twins: Real-time race car replicas ingesting live sensor streams, enabling AI agents to propose pit-stop strategies with Monte Carlo tree search algorithms.
- Data Lake and BI: A unified data platform built on Snowflake for cross-discipline querying—linking aero loads, tire pressures, driver telemetry, and weather forecasts through Power BI dashboards.
Engineering Talent Pipeline: Training the Next-Gen
Motorsports remain GM’s premier hands-on lab for young engineers:
- Rotational Programs: 12-month stints alternating between track support, CAE simulation, and road-car vehicle integration teams.
- AI Skill Workshops: TensorFlow and PyTorch courses taught by in-house data scientists, culminating in a hackathon to build race-strategy bots.
- Cross-Functional Collaboration: Joint projects between powertrain, chassis, and software groups driving holistic vehicle performance improvements.
“Racing forces you to solve boundary-pushing technical problems under deadline pressure. Those engineers go on to design safer, more engaging road cars,” says Morris.
Looking Ahead: Cadillac’s F1 Ambitions
In late 2025, GM confirmed Cadillac’s entry into Formula 1, initially partnering with Ferrari’s hybrid unit—comprising a 1.6 L V6 turbo with MGU-K and MGU-H systems—before transitioning to a fully in-house powertrain by 2029. Key targets include:
- MGU-K Recovery: 120 kW kinetic energy harvesting on braking, integrated into a bespoke Electronic Control Unit (ECU) with ISO 26262 compliance.
- Thermal Efficiency: Waste-heat recovery via the MGU-H turbocharger motor/generator, contributing to a target brake thermal efficiency above 52%.
- Energy Storage: Lithium-ion pouch cell pack limited to 50 kg and 50 kWh, with high-conductivity busbars and active cell balancing for peak discharge rates up to 400 kW.
“The software development freedom in F1’s hybrid regulations accelerates our battery management algorithms, and the aero constraints push our CFD teams to innovate,” Morris adds.
As GM expands its footprint across NASCAR, IndyCar, IMSA, WEC, and F1, the fusion of electrification, AI, and cloud-based simulation cements motorsports as both a proving ground and a crucible for developing tomorrow’s vehicles and engineers.