3D-Printed Railway Shelter Built in Under 6 Hours
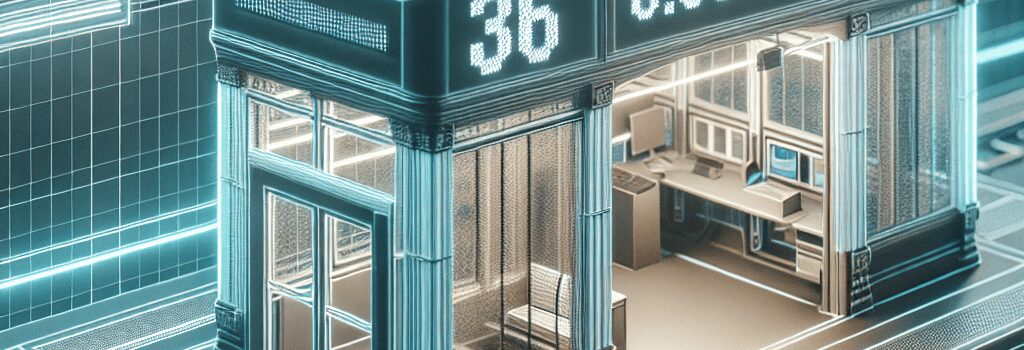
In a groundbreaking display of modern construction techniques, a custom 3D-printed railway shelter replaced an aging structure at Hatsushima Station in Wakayama Prefecture in less than six hours. This swift installation not only demonstrates the power of additive manufacturing but also paves the way for rapid infrastructure updates at remote transit stops.
Project Overview and Context
The station at Hatsushima serves the small town of Arida, with a population of approximately 25,000, known for its mandarin oranges and scabbardfish. Despite the modest daily ridership of about 530 passengers and a train frequency of one to three per hour, the station is integral to the community. The wooden shelter, once a staple of local travel, was outdated and in need of replacement. The project, spearheaded by construction firm Serendix in collaboration with West Japan Railway Company (JR West) and its venture capital arm, experimented with industrial-scale 3D printing to create a more economical and swiftly deployable solution.
Technical Specifications and Construction Details
The new shelter, designed as a trial for custom printed rail shelters, measures approximately 10 square meters (32 square feet) with a height of 2.6 meters (8.5 feet). Engineered with a layered mortar technique, the shelter was fabricated using a 3D-printing nozzle that applied a dull-green composite material, reinforced with steel bars and edged with precast concrete. According to JR West, this structure offers earthquake resistance on par with reinforced concrete houses while costing around half as much as traditional reinforced construction.
Assembly and Installation Process
The shelter was printed off-site and then transported in four modular parts via rail. The assembly process was exceptionally fast; reports vary slightly between a completed assembly time of just under three hours and six hours, as witnessed by on-site observers. By the time the first train arrived at 5:45 a.m., teams had successfully pieced together the structure. Although its current state is preliminary, pending the installation of ticket machines and other finishing touches, a full operational launch is anticipated by July, as reported by the Japan Times.
Industrial 3D Printing: A Game Changer for Rural Infrastructure
This innovative project highlights the potential of 3D printing in the realm of public infrastructure. Traditional construction methods can take days or even weeks for such installations, particularly in remote locations where workforce mobilization and material logistics pose significant challenges. 3D printing streamlines these processes through pre-fabrication and modular design, reducing labor requirements dramatically. Ryo Kawamoto, president of JR West’s venture capital arm, emphasized the reduction in manpower as a key benefit of this technology, which could help maintain rural railway stations more sustainably and economically.
Technical Analysis and Expert Opinions
Experts in additive manufacturing and civil engineering are taking a keen interest in this project. By leveraging high-precision robotic arms and specialized 3D-printing mixtures that include polymer additives and steel reinforcement encapsulated in mortar, the construction team ensured that the shelter maintained structural integrity even under seismic stress. The integration of embedded digital sensors for structural health monitoring is also under consideration for future iterations. These sensors would provide real-time data on stress distribution and potential material fatigue, allowing for predictive maintenance and ensuring passenger safety.
Future Implications for Rail Infrastructure and Beyond
The success of the Hatsushima Station shelter installation may set a precedent for the modernization of numerous similar rural transit hubs not only in Japan but globally. As urban areas face declining populations and aging infrastructure, combined with a growing need for rapid, cost-effective updates, 3D printing offers a viable alternative. The technique’s flexibility also opens up opportunities for customized designs that can reflect local aesthetic elements—illustrated by the mandarin orange and scabbardfish embossments found on the shelter—further strengthening community ties to these facilities.
Key Technical Specifications
- Dimensions: 10 sqm (32 square feet) area and 2.6 meters (8.5 feet) in height
- Material: Layered mortar composite with embedded steel reinforcement and a concrete frame
- Seismic Performance: Comparable to reinforced concrete structures
- Cost Efficiency: Approximately 50% cost reduction compared to conventional methods
- Assembly Time: Between 3 to 6 hours on-site
Conclusion
This rapid deployment project not only underscores the increasing viability of 3D printing in the construction sector but also points to broader applications in modernizing public infrastructure. With continuous advancements in materials science and robotic printing technologies, such innovations could revolutionize the way we approach construction projects, particularly in underserved or remote communities.