SpaceX Advances Reusability: Flight-Proven Super Heavy Booster Nears Reflight
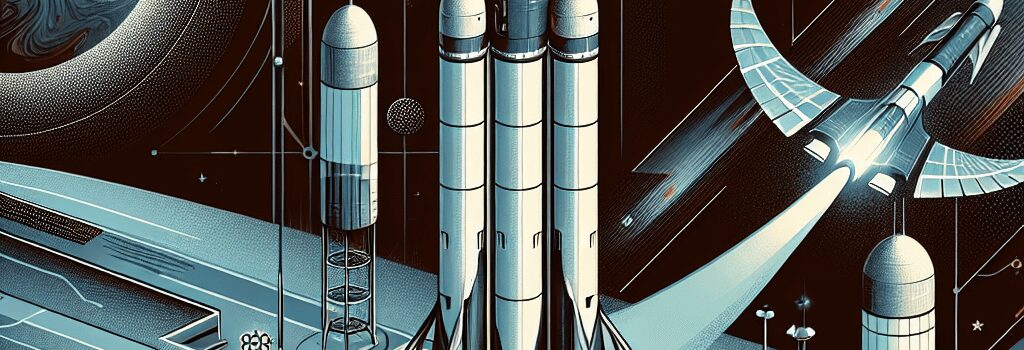
At 9:40 AM local time on Thursday at SpaceX’s Starbase launch site in South Texas, a major milestone was achieved for reusability in spaceflight. The company fired up a Super Heavy booster that has already flown to the edge of space, producing a noticeable burst of orange exhaust over approximately eight seconds. This static fire test marks the first time a “flight-proven” booster, designated Booster 14, has been reactivated, hinting at its potential for an imminent reflight and setting the stage for a new era in rapid rocket turnaround.
Super Heavy Booster: Technical Overview
The Super Heavy booster is one of the most complex and powerful rocket stages ever designed. With 33 methane-fueled Raptor engines at its core, the booster can produce nearly 17 million pounds of thrust—almost double the output of NASA’s historic Saturn V rocket. To put its scale into perspective, imagine the fuselage of a Boeing 747 standing on end. This immense structure is not only a marvel of engineering but also a crucial component of the Starship system that towers at 404 feet (123.1 meters) when combined with the upper stage.
- Engine Configuration: 33 advanced Raptor engines
- Thrust: Nearly 17 million pounds
- Overall Stack Height: 404 ft (123.1 m)
- Fuel: Liquid methane and liquid oxygen
Flight History and the Road to Reusability
Booster 14, which completed its maiden flight on January 16, is now under scrutiny following its recent static fire test. Its successful ignition suggests that the booster is closer than ever to being ready for a reflight—an accomplishment that would reinforce SpaceX’s ongoing commitment to reusability. Historically, SpaceX refined this model with its Falcon 9, which has been re-flown 426 times after months of comprehensive inspection and refurbishment. However, the Super Heavy booster, with its added size and engine density, presents a more formidable challenge.
Unlike Falcon 9 boosters, which are transported from recovery sites via drone ships and trucks to inspection facilities in Hawthorne, California, the Super Heavy booster remains largely onsite at Starbase. This strategic decision streamlines the refurbishment process and reduces turnaround time. Technical upgrades and lessons learned from the Falcon 9 program have been integrated into the Super Heavy design, allowing SpaceX to push the envelope even further with reusability goals.
Implications for Future Missions and Cost Reductions
The successful static fire test of Booster 14 could signal a paradigm shift for future Starship launches. Reusing a booster that has already been flight-proven can slash operational costs and support the ambitious 2025 goal of up to 25 Starship flights. With each successful test, SpaceX not only refines its booster technology but also validates its in-house processes aimed at rapid reuse and turnaround.
Technical advancements in telemetry and sensor data collection during these tests ensure that engineers can quickly pinpoint potential issues, optimize engine performance, and validate structural integrity. These insights are invaluable as SpaceX prepares to meet not just commercial launch demands but also high-profile missions, including NASA’s Artemis lunar program and expansive Starlink satellite deployments.
Challenges with Starship’s Upper Stage
While Booster 14 shows promising progress, the Starship upper stage—simply known as the ship—continues to face significant engineering challenges. Recent test flights in January and March involving the Block 2 or Version 2 ship saw catastrophic failures approximately eight minutes after launch. The primary issue appears to be an unexpected loss of engine power and vibration-induced structural stress, which led to the vehicle tumbling and ultimately disintegrating during reentry.
The Federal Aviation Administration (FAA) has concluded its investigation into the January failure, citing increased in-flight vibrations as a probable cause along with subsequent stress and hardware failure in the propulsion system. Although SpaceX has implemented 11 corrective measures following that incident, the cause of the March failure remains under investigation. These setbacks underscore the complex interplay of thermal, mechanical, and fluid dynamics challenges in reentering Earth’s atmosphere.
Industry Expert Opinions and Further Technical Analysis
Leading aerospace analysts have applauded the successful testing of the flight-proven booster. They highlight that the integration of advanced sensor arrays and real-time telemetry during static fires is crucial for validating performance under extreme conditions. According to one veteran aerospace engineer, “Reusing a flight-proven booster is a transformational step, as it significantly reduces mission costs and improves turnaround times. The real-world data gathered during these tests will be key to advancing our understanding of high-thrust operations.”
Furthermore, experts suggest that the innovations seen in the Super Heavy booster, including its rapid refurbishment approach and the use of mechanical arms for precise landing, could set new industry standards. As these methods mature, they not only validate the booster’s design but also provide strategic insights that could enhance future spacecraft development across the commercial space sector.
Recovery, Refurbishment, and Operational Readiness
One standout aspect of the Super Heavy program is its departure from traditional refurbishment techniques used in the Falcon 9 era. The booster’s design incorporates a host of improvements based on iterative testing and operational experience. By keeping the booster on-site at Starbase and avoiding the logistical complexities of long-distance transportation, SpaceX is cutting down both costs and processing times.
In contrast to Falcon 9’s extensive refurbishment process that involved truck rolls between landing sites, inspection facilities, and test stands, the new system is optimized for efficiency. With automated diagnostic tools and precision engineering, future recovery and refurbishment cycles may be reduced to a timespan of mere weeks—a critical advantage for high-frequency launch schedules.
Looking Ahead: The Future of the Starship Program
As SpaceX scrutinizes both its booster and upper stage technologies, the next Starship launch remains uncertain with regard to whether it will feature a refurbished Booster 14 or a new unit from the production line. However, the progress on the Super Heavy booster instills optimism that reusability strategies are on track to fundamentally reshape orbital launch economics.
This evolution is especially critical for the Artemis lunar program, which depends on multiple Starship refueling flights to support lunar landings and eventual missions to Mars. A faster and more reliable booster reusability cycle is key to meeting both commercial and governmental launch windows amid rising global competition in space.
Conclusion
SpaceX’s recent test of a flight-proven Super Heavy booster underscores a significant leap in the company’s reusability strategy. While challenges remain—particularly with the Starship upper stage—the advancements in booster technology, refurbishment efficiency, and rapid reflight potential are setting the course for a new era of cost-effective, high-frequency space missions. As SpaceX continues to iterate on its designs and processes, industry experts remain cautiously optimistic about the future of the Starship program and its impact on both commercial spaceflight and deep space exploration.
The coming months will be critical as SpaceX aims to merge these incremental advancements into a cohesive operational strategy, potentially marking a dramatic shift in how we approach large-scale space missions.
Source: Ars Technica