14 Technical and Economic Reasons Why Tariffs Fail to Reanimate U.S. Manufacturing
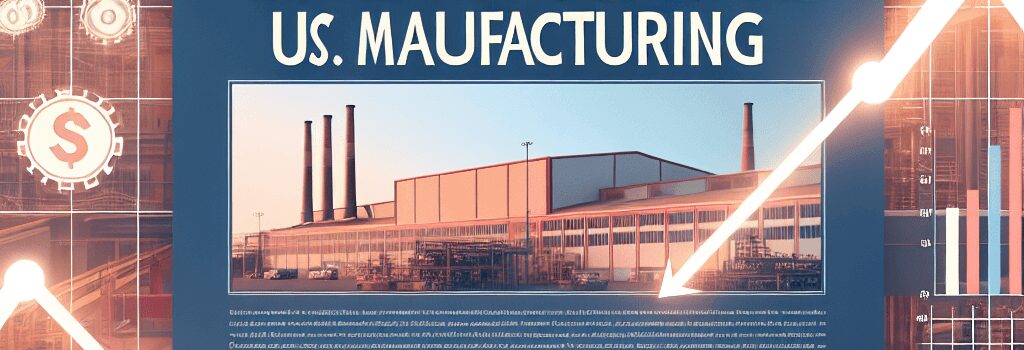
The recent imposition of steep import taxes ranging from 10% to 49% by the administration has reignited a long-standing debate about whether tariffs can bring back manufacturing to the United States. At its core, this policy is founded on a misunderstanding of the complexities of modern industrial production. In this article, we delve into 14 detailed reasons—with numerous technical insights and further context—illustrating why these tariffs might not only fail to restore manufacturing dominance, but could also render American products more expensive and less competitive on a global scale.
1. They’re Not High Enough
Consider the example of the iPhone 15: it is assembled in both China and India due to highly optimized supply chains and lower production costs, even in the face of tariffs. In technical terms, a tariff acts as an additional cost layer in the bill of materials. For instance, if an iPhone component costs $100 and a 54% tariff is applied, the component now costs $154 to import. Assuming a standard double markup in the distribution chain, the final cost hikes exponentially. The disparity in production cost remains significant when the U.S. wage base, regulatory and logistics inefficiencies are factored in, leaving domestic manufacturing uneconomical even with punitive tariffs.
2. America’s Industrial Supply Chain is Underdeveloped
While the U.S. consumer market benefits from an efficient retail distribution network, the industrial supply chain—vital for assembling products like smartphones or automobiles—is largely offshored to Asia. Modern manufacturing necessitates rapid procurement of specialized parts such as glass panels, semiconductor chips, and high-precision mechanical components. U.S. factories, facing a shortage of local suppliers for these components, would invariably rely on overseas vendors. Even if tariffs were to raise import costs, the lead times and logistical reliability of Asian supply chains (backed by decades of developed infrastructure) will remain the more attractive option for companies under pressure to keep production efficient.
3. Inadequate Domestic Technical Know‐How
Manufacturing modern electronics and complex machinery is a science in itself. For example, fabricating state-of-the-art semiconductors requires cleanroom environments, advanced photolithography systems, and process control algorithms that are currently not widely available in the United States. Even with generous financial incentives, recreating the technical ecosystem found in Taiwan’s TSMC or South Korea’s semiconductor hubs would take years, if not decades. Beyond semiconductors, specialized industries—ranging from precision-mold making for plastic toys to composite material fabrication—face similar challenges due to decades-long knowledge shrinkage in core areas of manufacturing engineering.
4. The True Cost of Labor Remains Competitive Overseas
Although high wages are frequently cited as the reason for offshoring production, a detailed assessment shows that Chinese labor, for instance, is not merely cheap but also efficient. Labor cost is compounded by cultural work ethics, rigorous training, long hours, and performance-driven practices. Moreover, automation integrated with human dexterity in Asian manufacturing lines has propelled productivity while reducing per-unit costs. U.S. labor markets, burdened with higher wage demands, regulatory complexities, and a litigious environment, simply cannot scale to meet the speed and cost efficiency observed abroad without a radical restructuring of worker skill sets.
5. Outdated Domestic Infrastructure
Manufacturing is not solely about machinery and labor—it demands robust infrastructure. The U.S. has seen stagnant electricity generation per capita compared to surging output in industrializing nations. Modern assembly lines also require efficient logistics, from upgraded highways and seaports to modern power grids and dedicated industrial parks. For example, the supply chain for electronic components in Asia is reinforced by specialized industrial zones that include on-demand energy supplies and integrated transport logistics, unlike the dispersed and aging infrastructure in many parts of the U.S.
6. The Time Horizon for ‘Made in America’ is Too Long
Building a new factory in the U.S. is a long and capital-intensive process. Beyond acquiring permits, establishing supply contracts and hiring specialized talent, the fabrication and commissioning of production lines span at least a two-year window. This delay, compounded by the current tariff-induced volatility, undermines investor confidence. By the time a domestic facility becomes fully operational, political priorities may have shifted entirely, leaving manufacturers in limbo.
7. Uncertainty and Complexity of Tariff Regulations
The rapid changes in tariff policies create a highly unstable environment for planning large capital investments. An importer or manufacturer must now navigate a labyrinthine system, combining original import duties with additional charges—such as the ‘fentanyl tariff’ or rotational tariffs on goods from specific countries. This uncertainty prevents businesses from accurately forecasting costs, which in turn stifles local manufacturing expansion. Many firms have already delayed or cancelled projects, diverting capital towards less risk-intensive overseas operations.
8. Cultural Aversion to Manufacturing Work
The modern American workforce has shifted away from manual assembly and industrial labor in favor of roles in services and innovation. Manufacturing is perceived as physically demanding and less prestigious, which hinders the nationwide availability of skilled labor. Although nostalgia for traditional manufacturing exists, the reality of long hours, physically taxing work, and secondary socioeconomic challenges such as local infrastructure degradation makes it less appealing.
9. Shortage of Skilled Labor and Management
With a surplus of human resources in countries like China, the U.S. faces a dual challenge: not only is manual labor in lower tiers less abundant, but there is also an acute shortage of managers experienced in modern manufacturing techniques. The brain drain to the tech and financial sectors further exacerbates the lack of domestic expertise necessary for revitalizing U.S. production lines.
10. Automation Isn’t a Panacea
While many tout automation as the solution to high labor costs, the technological leap required for full-scale automation in manufacturing is non-trivial. Though industrial robots are finding increasing applications, the U.S. currently lags behind China in both the installation rate and cost-competitiveness of these robots. Moreover, not all manufacturing tasks can be automated reliably, especially those requiring nuanced assembly or quality control in a dynamically adapting production process. This leaves American industries vulnerable in sectors where human-machine collaboration is essential.
11. The Increased Risk of Litigious Challenges
The U.S. legal and regulatory environment makes domestic manufacturing a double-edged sword. Companies here face the constant threat of costly lawsuits and regulatory compliance challenges that do not impact their overseas counterparts. This litigious culture further drives investors toward locations where legal risks are minimized, allowing companies to streamline operations without the risk of sudden financial penalties or operational disruptions.
12. Uneven Enforcement and Policy Manipulation
Enforcement of tariffs is subject to manipulation and inconsistent application. For instance, a U.S.-based importer might find itself facing severe penalties for under-declaring the value of goods, while a similar issue by an overseas partner might be overlooked or met with just minor sanctions. This double standard not only creates an uneven playing field but may also encourage tax evasion practices among domestic companies, further undermining the intent of the policy.
13. Tariff Structures Target the Wrong Parts of the Supply Chain
The recent tariff policy applies uniformly to both raw components and finished goods. This lack of nuance is fatal to complex manufacturing processes which rely on affordable and timely access to intermediate inputs. By taxing components along with finished products, the policy inadvertently raises production costs for any domestic manufacturer attempting to assemble goods from imported parts, effectively strangling innovation and growth in this sector.
14. Historical Missteps and the Michael Jordan Analogy
Much like Michael Jordan’s foray into baseball—where his skill transfer was limited—the assumption that tariffs alone can reshape a deeply entrenched manufacturing ecosystem is misguided. The historical record shows that transformative changes in national industry require more than just punitive fiscal measures; they demand a robust foundation of skilled labor, technology, and infrastructure that cannot be built overnight.
Additional Analysis 1: The Role of Advanced Robotics and AI in Manufacturing
Emerging technologies, including artificial intelligence, machine learning, and advanced robotics, have redefined modern manufacturing. In countries like China, the integration of customized industrial robots into the production line has led to improvements in quality, speed, and cost efficiency. In contrast, U.S. manufacturing struggles with outdated automation protocols and slower adoption of smart robotics. Expert opinion suggests that rather than imposing tariffs, investment in industrial IoT, predictive maintenance, and real-time analytics could revitalize production efficiencies and help bridge the gap between domestic and overseas competitors.
Additional Analysis 2: Leveraging Cloud-Based Supply Chain Solutions and Digital Twin Technology
Innovative approaches such as cloud-based supply chain systems and Digital Twin technology present a promising alternative to relying solely on tariffs for domestic rejuvenation. These systems allow companies to simulate and optimize production processes virtually, thereby reducing downtime and improving operational efficiency. By embracing such digital technologies, U.S. manufacturers can better manage complex logistics, coordinate with a decentralized network of suppliers, and mitigate risk due to sudden policy shifts. Several tech start-ups and innovation hubs in Silicon Valley are pioneering these solutions, which could form the backbone of a more resilient manufacturing ecosystem.
Additional Analysis 3: Policy Solutions and Expert Recommendations
Industry experts advocate for a gradual and structured implementation of tariff policies, combined with targeted investments in workforce education, infrastructure modernization, and technology adoption. They suggest adjusting tariffs selectively—imposing higher duties on finished goods while offering concessions for critical components and advanced machinery. Furthermore, incentives such as manufacturing visas for technical experts, duty drawbacks for export-oriented production, and streamlined regulatory processes can create a more predictable environment, encouraging long-term investments in domestic manufacturing.
Conclusion and Final Thoughts
The overarching goal of reviving America’s manufacturing sector is commendable and, if executed properly, can lead to a reinvigorated economy and a robust industrial base. However, the blunt tool of across-the-board tariffs is neither effective nor efficient. It risks exacerbating supply chain issues, increasing production costs, and ultimately weakening our competitive position in the rapidly evolving global market.
For America to truly emerge as a global manufacturing leader, foundational reforms are necessary. Priorities should include modernizing industrial infrastructure, embracing advanced automation and AI, bolstering workforce skills, and implementing tariff policies that are nuanced and predictable. The future of manufacturing depends not on punitive measures but on innovation, strategic investments, and a comprehensive understanding of modern global supply chain dynamics.
- Economic Resilience: Restoring domestic production capabilities strengthens national security by reducing reliance on foreign supplies in critical sectors.
- Innovation and R&D: A vibrant manufacturing base promotes research and development, essential for breakthroughs in fields like renewable energy, cybersecurity, and artificial intelligence.
- Social Benefits: Revitalizing high-end manufacturing can create sustainable, well-paying jobs, ensuring that America’s diverse talent pool is fully utilized.
In summary, while tariffs might seem like a quick fix, they are insufficient to catalyze the complex transformation required to reestablish U.S. manufacturing supremacy. A multifaceted approach—integrating technology, infrastructure investment, and skill development—is the only viable path forward.