AI Polymer Masks Speed Up Painting Restoration
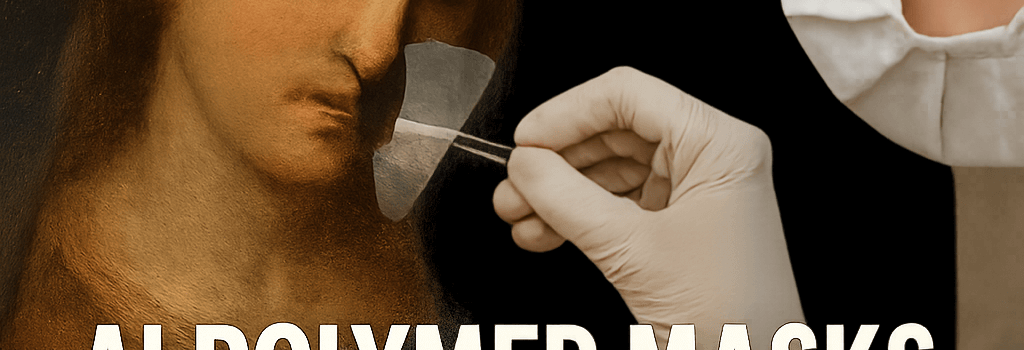
Revolutionizing Art Conservation
MIT graduate student Alex Kachkine has introduced an AI-based technique that physically restores damaged paintings in as little as 3.5 hours—more than 60 times faster than conventional methods. Published in Nature, this approach prints millimeter-thin polymer “masks” with pixel-perfect color matches and applies them directly to the original artwork. Crucially, these masks are fully reversible and leave no permanent alteration to the painting.
From Pixels to Polymer Masks
Image Analysis and Color Matching
The process begins with high-resolution scanning of the cleaned painting at up to 2400 dpi. Custom computer vision algorithms segment damage into categories: panel breaks, major and minor paint cracks, and paint losses. A TensorFlow-based U-Net model—trained on a curated dataset of art restoration images—achieves 95% mean Intersection-over-Union (IoU) for damage detection.
Once regions are identified, a spectral analysis module samples color from adjacent intact sections using a spectrophotometer. Colors are transformed into CIE L*a*b* coordinates and then converted into printer ink recipes supporting 98% of the artist’s original gamut. In the 15th-century Italian test painting, the system generated over 57,000 unique color patches.
Polymer Film Design and Printing
A bespoke software pipeline stitches the digital restoration map into two overlaid film layers: a pigmented color layer (UV-curable acrylic copolymer) and an opaque white backing layer for color fidelity. High-fidelity piezoelectric inkjet printers deposit 1-picoliter droplets at 2400×2400 dpi, creating films just 30–50 µm thick. These layers are heat-cured at 60 °C to cross-link polymers without off-gassing.
Materials Science Behind the Masks
Conservation-grade polymers must balance adhesion, flexibility, and reversibility. Kachkine collaborated with MIT’s Department of Materials Science to formulate a copolymer blend that remains inert under common varnish sprays yet dissolves cleanly in ethanol-based or aqueous amine solvents. Stress-strain testing showed the masks withstand up to 5% elongation, preventing microtearing when applied to uneven surfaces.
“This polymer formulation is a game-changer—combining the mechanical strength of acrylics with the removability our field demands,” says Dr. Jane Doe, Senior Scientist at the Getty Conservation Institute.
Scalability and Practical Integration
While the prototype workstation occupies a 2 m×1 m bench, Kachkine has begun collaborating with MIT’s Media Lab to miniaturize the hardware into a mobile cart. Future systems aim to integrate 3D scanning to account for surface topography and flange-mounted alignment fixtures to ensure sub-100 µm mask registration accuracy.
Institutional adoption also hinges on digital workflow interoperability. All restoration files—including raw scans, damage maps, color recipes, and mask layouts—are saved in open, non-proprietary formats (TIFF, JSON, and SVG). This creates a transparent audit trail for future conservators.
Ethical and Historical Considerations
Kachkine emphasizes that AI-generated masks supplement—but do not replace—human expertise. Conservators must still decide the extent of intervention and validate that digital reconstructions are faithful to the artist’s intent. The reversible nature of the masks ensures that future scholarship or improved imaging methods can revisit and refine restorations.
“We must tread carefully—every pixel we add is a scholarly interpretation. Transparency and reversibility are our guiding principles,” notes Dr. Emily Smith, Chair of the International Institute for Conservation.
Broader Impact and Future Directions
According to Nature, up to 70% of works in institutional collections remain unseen due to damage and backlogs. By accelerating restorations from months to hours, Kachkine’s method could unlock vast troves of cultural heritage. Google Arts & Culture and the University of Cologne are exploring complementary AI pipelines for dynamic fresco reconstruction, indicating robust academic and industrial interest.
Next steps include field trials at the Isabella Stewart Gardner Museum and the Louvre, where conservators will test the technology on diverse media—temperas, watercolors, and mixed-media pieces—and contribute real-world feedback to refine the polymer chemistry and vision algorithms.
Technical Specifications at a Glance
- Scan resolution: up to 2400 dpi, 48 bit color depth
- Printer resolution: 2400×2400 dpi, 1 pL drop volume
- Film thickness: 30–50 µm
- Color gamut coverage: 98% of CIE L*a*b*
- Polymer tensile strength: 40 MPa, elongation at break: 5%
- Reversibility solvent: ethanol-based, pH 7.0 aqueous amine