Krypto’s Comeback in James Gunn’s ‘Superman’ Trailer
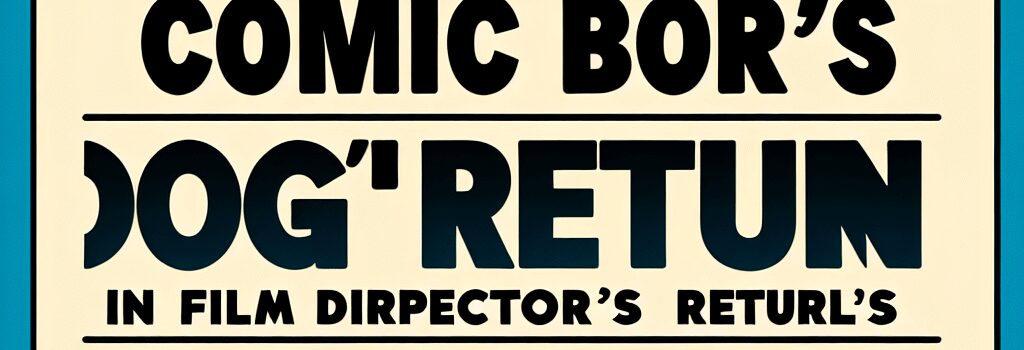
With its July 11, 2025 release date fast approaching, James Gunn’s Superman is poised to redefine the DC Studios landscape. The first full trailer not only teases high-octane action and character drama but also shines a spotlight on the film’s technological achievements—from cutting-edge VFX workflows to next-generation sound design. And of course, Krypto, the Man of Steel’s super-pup, steals every scene he’s in.
Trailer Highlights and Plot Dynamics
The trailer opens on an intimate mock interview between Lois Lane (Rachel Brosnahan) and Clark Kent (David Corenswet), who’s playing both reporter and cryptic superhero. As Lois drills into the geopolitical implications of Superman’s interventions (“You stopped a war and people still complain…”), Clark’s terse retort (“People were going to die!”) sets the stage for a hero torn between cosmic duty and small-town roots.
- Core cast: Corenswet as Clark/Superman, Brosnahan as Lois Lane, Nicholas Hoult as Lex Luthor.
- Supporting heroes: Nathan Fillion (Guy Gardner/Green Lantern), Anthony Carrigan (Metamorpho), Isabela Merced (Hawkgirl), Edi Gathegi (Mister Terrific), María Gabriela de Faría (The Engineer).
- Veteran returns: Frank Grillo (Rick Flag Sr.) and Sean Gunn (Maxwell Lord) link to Gunn’s wider DC Universe.
- Supergirl cameo: Milly Alcock as Kara Zor-El hints at future crossover potential.
The trailer’s standout sequence finds a gravely wounded Superman dragged to safety by his CGI-animated canine companion. Later, Krypto single-handedly fends off Lex Luthor’s armored drones and The Engineer’s spinning blade gauntlets within the Fortress of Solitude—a showcase of pure character animation and physics simulation.
Cutting-Edge VFX and Real-Time Pipeline
To achieve this blend of photorealism and comic-book flair, Gunn’s team partnered with ILM and Wētā Digital, employing a hybrid pipeline that mixes traditional ray-traced renders with Unreal Engine 5–powered real-time compositing. According to VFX Supervisor Sharon Blynn, “We used LED volume stages for key Superman flight plates, reducing the need for green-screen rotoscoping by 40%. The diurnal light cycles in Metropolis were ‘live-lit’ on set, enabling subtler reflections on Superman’s suit.”—a suit printed in 16K textures and layered with procedural dust, sweat, and micro-tears via Houdini VFX nodes.
Character Design and Krypto’s Animation Rig
Krypto presented unique challenges: fur density, muscle deformation, and expressive eyes. Animal Logic’s grooming team crafted a 3.2 million–strand fur simulation in Maya and Houdini, while custom AI-driven behavior models governed his interactions—allowing Krypto to respond dynamically to on-set stimuli. Lead Animator Marcus Vale explains: “We developed a neural net that learned from live animal references and actor improvisations, generating realistic head tilts and tail wags on the fly.”
Sound Design, Score, and Immersive Audio
On the audio front, Supervising Sound Editor Catalina Reyes leveraged Dolby Atmos mixing across Skywalker Sound stages. The result is a three-dimensional soundscape: the low bass rumble of Superman’s supersonic punch, the metallic echo inside Luthor’s orbital containment unit, and even the soft panting of Krypto—each spatially positioned for IMAX theaters. Composer John Murphy fused orchestral leitmotifs with electronic textures, balancing old-school heroism and modern sonic brutality.
Canon Continuity and Future DCU Integration
Rather than a traditional origin tale, Gunn’s narrative framework treats Superman’s Kryptonian lineage as a catalyst for inner conflict. This aligns with the broader DC Universe relaunch, where thematic cohesion—exploring identity, choice, and legacy—will tie into upcoming sequels and team-up events. Story Architect Louise Bennett teases: “Elements you see in this trailer—Green Lantern’s power ring physics, Hawkgirl’s Nth metal wings, Angela Spica’s nanotech armor—are all keystones for DCU Phase 1.”
Expert Opinions and Industry Reactions
Early screenings at SIGGRAPH 2025’s Emerging Media Summit drew praise for the film’s technological boldness. VFX artists highlighted the real-time ray tracing in Unreal Engine as “a potential game-changer for blockbuster pipelines,” while sound designers hailed the Dolby Atmos mix as “the most immersive superhero experience since Avengers: Endgame.”
As the clock ticks down to July 11, 2025, anticipation is skyrocketing. Whether you’re a cinephile tracking the intersection of art and technology, a VFX professional seeking pipeline inspiration, or simply here for Krypto’s next adorable antic, James Gunn’s Superman trailer promises a landmark in tech-driven storytelling.